As Seen on The Guardian: Weave a Supply Web as a Bridge to the Circular Economy
Such a web, made up of companies and organizations of all sizes, helps to keep items in use – and to create projects that benefit communities and the environment
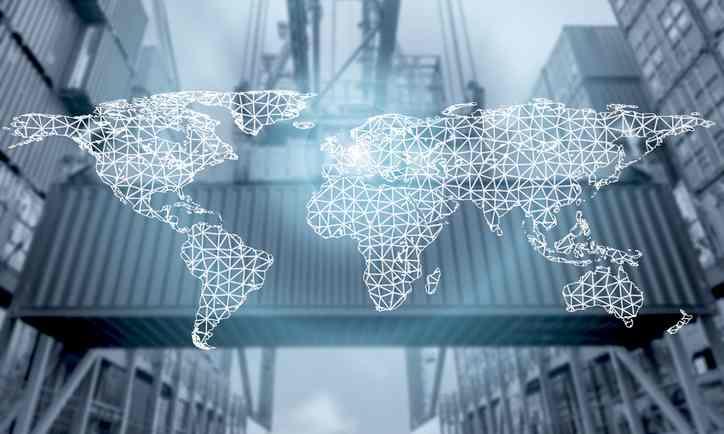
As Seen on The Guardian: Weave a Supply Web as a Bridge to the Circular Economy
A more sustainable future means advancing a circular economy – one that keeps material in use and creates jobs along the way. The way to get there lies in the collaboration of organizations of all sizes, in what we’re calling supply webs.
A supply web not only helps keep items in use, but also creates satellite projects that can benefit communities and the environment. For example, there’s General Motors’ Do Your Part initiative, in which small, medium and large companies recycle plastic bottles into fleece. That fleece is turned into car parts as well as insulation for coats made especially for the homeless. More than a dozen companies are involved, each one playing a different but critical role.
While a chain is only as strong as its weakest link, supply webs are dynamic and interconnected – built with additional strength to get tough projects done. By moving a material in different directions, more companies get involved. If one of those businesses fails or bows out, the rest of the initiative continues. As other extensions and more products develop, they increase the web’s size and impact, and ultimately boost community resilience.
Supply webs are even more resilient when done in cross-sector, collaborative ways. Those working outside their sectors can share new best practices. Ideas can be exchanged and products developed simply by talking about challenges and opportunities. This is typical of many companies committed to sustainability.
To build a circular economy and create a more resilient community, there must be greater collaboration. Beyond the manufacturing sector, this means nonprofits; government officials; small, medium and large businesses; academia; and concerned citizens.
Companies and organizations of all sizes need to challenge themselves to continually improve and find better homes for their waste. Sometimes that entails thinking beyond a single material to join two or more items to create a new product. Obviously a market and demand must already exist for the new product, or else be created. Then a person or company can be linked with someone who has the material, spurring transactions and other economic opportunities.
The Materials Marketplace is one platform that enables this movement of goods and materials. Several nongovernmental organizations (NGOs) have come together with business like GM to develop an online database that serves as an inventory list. The idea: one company’s byproducts can be another’s raw material. Not only are there environmental benefits; the material usually is obtained at a better cost than buying new. And the database links companies that may not have traditionally worked together in the past, so they can create innovative collaborations.
The four steps key to building a supply web:
1 Get further engaged in your supply base. Understand the flow of materials and the steps involved in processing them. This way, you can better steer the project and bring sustainability-minded companies together to share their perspectives and ideas for additional process improvements.
2 Understand all project steps. Act like you’re a general contractor, with a need to understand all phases of construction to ensure a solid final product.
3 Think beyond the product’s first life. While developing a project, anticipate and plan for the final product’s second incarnation and how that can grow into other links to further develop local economies and communities.
4 Keep it local. Each step in a manufacturing process allows for continued economic development and for technical knowledge to stay within a community. Webs can expand in many directions, but distances should remain as tight as possible. Today, many materials entering their second lives are sent for processing outside of the country that generated them. This is a missed economic opportunity, as each processing step increases the material’s value and can spur job growth.
Companies shouldn’t just keep material in use. They should also look at its economic value, societal impact and benefit to the company in the long term.
John Bradburn is GM’s manager of waste reduction
Reposted from TheGuardian.com/General-Motors-Partner-Zone with permission.