One-of-a-Kind Facility Shapes R&D Breakthroughs
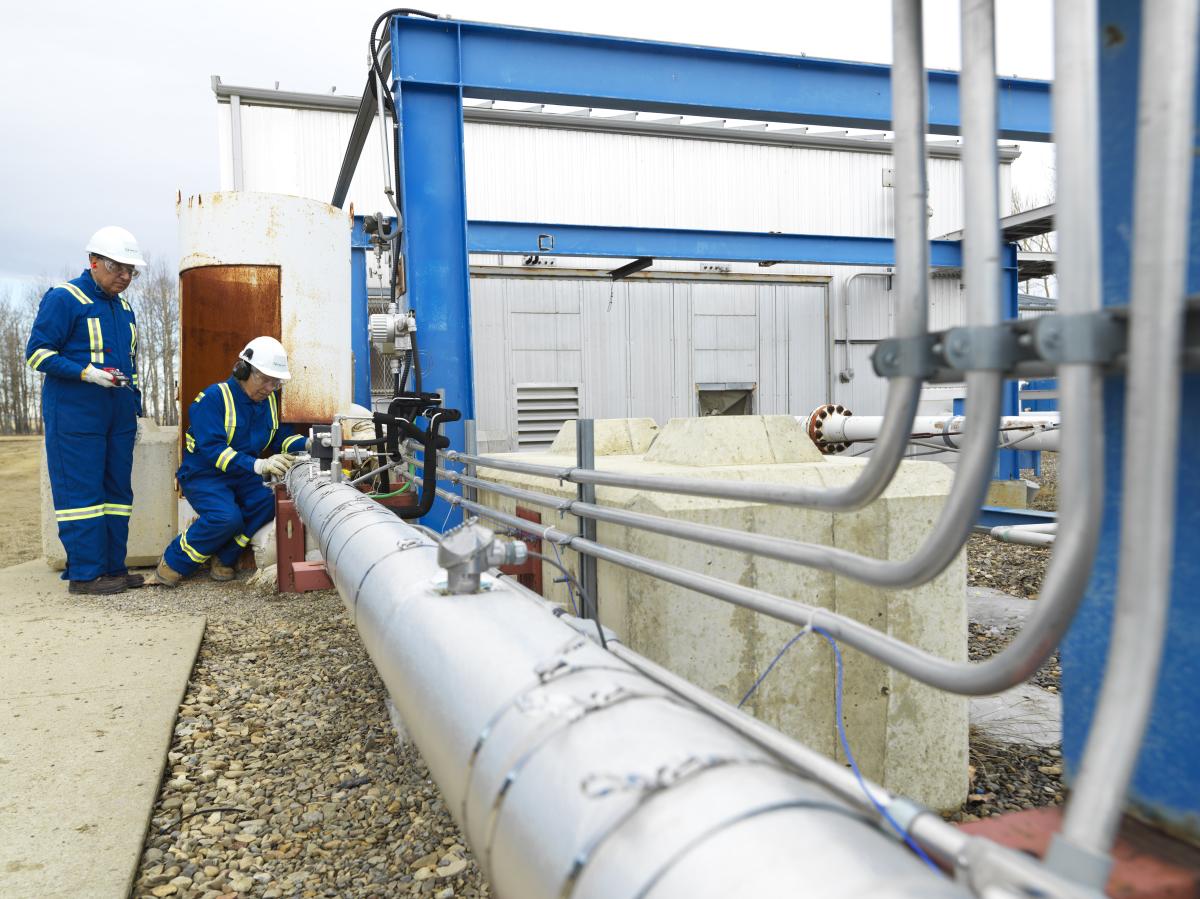
They’ve come from UK, Japan, China, Australia and Brazil because it is a ground-breaking piece of equipment – the only one of its type in the world.
They’ve come out to TransCanada’s Gas Dynamic Test Facility, located in Didsbury, Alberta to view the results from a relatively recent addition to TransCanada’s research and development (R&D) program– a $300,000 high pressure shock tube that replicates, with a high degree of accuracy, the events following a rupture in a high-pressure natural gas pipeline.
Operating at between 5000-5800 psi, the shock tube provides valuable information about pipeline design and material strength that is used to build safe and reliable pipelines. And in the unlikely event of a rupture, it also helps reduce the impact on local communities by ensuring the size of the affected site is contained to the smallest possible area.
“TransCanada built this shock tube at the Didsbury facility, which is capable of testing all kinds of natural gas mixture compositions,” says Kamal Botros of NOVA Chemicals. “We also control gas pressure, temperature and the degree of richness of the gas mixture, then we simulate a rupture in the most cost effective and accurate way”.
Old facility contributes to new technologies
Formerly a working TransCanada compressor station, the Didsbury facility has been the scene of some of the finest moments of TransCanada’s R&D efforts.
The site, built by TransCanada back in 1984 with research conducted in partnership with NOVA Chemicals Centre for Applied Research – is the historical home to the first above ground full-scale natural gas test loop in the world.
“It’s the first one of its kind in mimicking the actual operations of high pressure gas flow in piping elements and full-scale compressor station,” says Botros, who has spent 32 years researching and understanding the workings of compressors and related equipment to ensure optimum efficiencies and improved performance and reliability.
“Others tried a similar facility in the United States following our layout, but they use stored gas, whereas we are the only ones that use gas right from the TransCanada system – the same pipeline-quality gas you get at home – to conduct all of our research activities.”
The Didsbury test facility includes complex above ground pipelines, blow down facilities, pressure safety valves, gas metering and calibration equipment. All are live and can be reconfigured for any type of research project required at the time.
Some of the other breakthrough innovations discovered at the Didsbury facility include:
Software developed by TransCanada in 1996 to eliminate compressor breakdowns
Two decades ago, costly and service-disrupting compressor breakdowns were fairly common in the industry. High pressure gas coming through the lines and into compressors could sometimes create conditions that cause the compressor to surge and break down.
The problem was the type of recycle valves being used around the compressors, designed to relieve the pressure and bring it out of surge.
“Before 1996, compressor station designers would put any sized valve without understanding not only its appropriate capacity, but also its opening characteristics, opening time, control logic relative to the characteristics of compressors it is protecting – essentially you need the right valve for the right control and for the compressor in question,” said Botros.
He personally spent the better part of ten years experimenting and understanding the interaction between compressors and the recycle system.
“The results were that we developed a software in late 90’s, unique to TransCanada based on the information we learned and the technologies developed – and now we use those techniques and the know-how at all company compressor facilities operating on natural gas."
Blow down silencer was patented in the 1990’s
A blow down is the act of releasing natural gas from a section of pipeline so maintenance work can be done safely. The noise generated from this operation used to be extreme and was heard by residents living in surrounding areas.
TransCanada worked on a program to suppress the noise, and came up with a silencer that suppresses the sound by 40 decibels, or about 100 times over.
That invention created at the site was patented and implemented at many of our compressor stations, and became the norm for designing new stations and blowdown facilities.
Other examples of ground breaking research include a patented two-stage supersonic ejector to capture natural gas leakage from compressor seals, a flow loop used to simulated the impacts of impurities in CO2 pipelines used for carbon capture and storage, and testing of different designs of pulsation bottles to optimize pressure loss and improve the efficiency of reciprocating compressors.
It’s examples like these R&D breakthroughs that position TransCanada at the forefront of innovation to improve the safety and reduce the environmental impact of our operations. TransCanada has one of the industry’s largest R&D programs, investing over $38 million in R&D projects across North America in 2014, and more than $110 million over the past five years. Learn more about how the company ensures its assets are safe and reliable in the R&D section of the 2014 CSR Report.