Cultivating a Safety-First Mindset at Covia
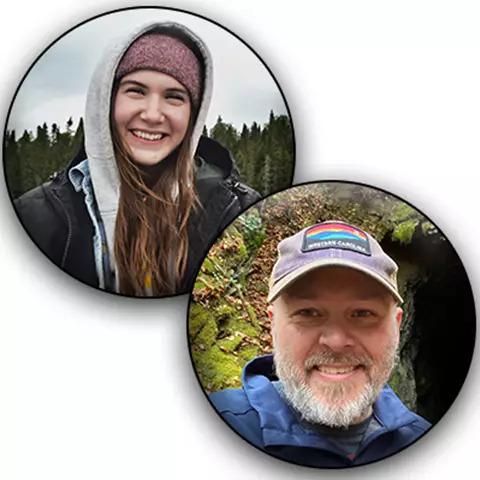
Cultivating a safe work environment plays a critical role in everything we do at Covia. From our plant locations to our offices – safety and health remain a consistent focus to ensure the well-being of our Team Members, customers, and communities.
In 2024, Covia continued to innovate our strategies and workflows to further improve safety for our team members. Read on to find out more about the important work our Safety and Health team has completed over the past year, a preview of upcoming safety innovations, and a closer look at Covia’s Safety Days.
Safety and Health Team Highlights: Chris Thynne & Mona Legin
Covia’s approach to safety is outlined in our Safety and Health Management System (SHMS) – a comprehensive collection of policies, guidelines, and procedures that help guide everything we do. Our Safety and Health team helps ensure Covia’s plants and locations are following the SMHS and creating the safe work environment that’s critical to our operation.
We want to highlight two members of the Safety and Health team who have helped in the implementation and management of recent key technologies. Chris Thynne, Safety and Health Manager, and Mona Legin, Ergonomics Specialist, are invaluable team members who have played important roles in our safety efforts.
Chris started working with Covia back in 1988 as a quality control and environmental supervisor. Over the years, he held several positions at Covia until landing in the safety and health department in 2011. He is currently part of the safety and health team.
Mona earned her bachelor’s in human resources and started working at Covia’s Quebec, Canada plant while still a student. During her seven-year career at Covia, she worked in a variety of roles at the plant level before being offered the position of corporate ergonomics specialist. In her current role, Mona monitors workplace ergonomics to help make a difference in the long-term musculoskeletal health of Covia’s employees.
Chris, Mona, and the safety and health team have worked diligently to implement innovative safety measures that further reduce the risk of injury in the workplace – including wearable safety sensors and digital workplace inspections.
Preventing Injury with Safety Sensors
In March of 2024, Covia started rolling out new safety sensors to team members at a select handful of locations. This self-coaching tool provides instant feedback to team members when the sensor detects “hazardous movements.” Movements that are flagged can include instances such as lifting a heavy object with the back instead of the legs. The goal of implementing these safety sensors is to help team members consider their body movements and act in a way that reduces the risk of developing a musculoskeletal disorder.
The sensors, which are clipped to the collar or arm of team members on the plant floor, flags any back or shoulder movement that puts them at risk. When a hazardous movement is flagged, the sensor buzzes and provides feedback on how to correct the movement. The data from these movements is then collected so members of the safety and health team can pinpoint where improvements need to be made to provide a safer work environment for the team. This process allows for preventative maintenance to lower the risk of injury.
“Sensor implementation has been very exciting,” Mona said. “I race in to check the sensor dashboard every morning to see the decrease in hazardous movements detected. It’s one of the highlights of my day.”
Covia initiated its exploration into wearable sensors. The process gained momentum when Mona joined the ergonomics team. One of her initial responsibilities was to research different sensors on the market and find one that can meet Covia’s unique needs. Since then, Mona has worked closely with the sensor representative to launch the program across several Covia plants.
“I’m looking forward to expanding the program to every employee, so they know how to keep their body safe,” she said. Covia plans to continue rolling out this innovative safety feature to all our plants.
The National Institute for Occupational Safety and Health (NIOSH) recently recognized Covia, in partnership with Soter Analytics, for the implementation of our wearable sensor program by awarding us with the Mine Safety and Health Technology Innovations Award. When presenting the award, NIOSH noted that Covia demonstrated an exceptional commitment to leveraging technology in innovative ways that exceed regulatory standards, thereby improving the safety and health of our employees.
Streamlining Safety with Digital Workplace Inspections
The safety and health team has been hard at work preparing a digital mobile equipment inspection pilot to start later this year. By utilizing a digital workflow and tablets for inspections, Covia can ensure proper inspections are completed and the correct actions taken.
One advantage of a digital system over traditional pen and paper is that the safety and health team can enforce SMHS procedures more effectively – providing additional insight on a regular basis to review risk and potential defects in a piece of equipment.
Digital workplace inspections would ensure team members could not start working on a project until the proper work permits are filed, the SLAM risk assessment is completed, and checks are in place before the project begins. This helps keep team members safe. With these new technologies, Covia can better utilize data to understand what’s happening so we can modify our programs or policies to better protect our team.
Covia is looking forward to implementing digital workplace inspections later this year.
Building a Safe Work Environment
Covia provides employees with regular training on our safety policies and procedures, including annual emergency action drills, as well as required role- or location-specific training, to ensure a proactive approach to incident preparedness and response applicable to each team member.
Part of that training includes the “Safety Starts with Me” program – an employee-led engagement initiative that helps to build rapport among team members to create a positive work environment at their plant.
“A safe work environment comes down to workplace culture,” Mona said. “It comes from experience and strong communication.”
The program stems from the idea that everyone at the plant is on the same level – there is no hierarchy when it comes to safety. All team members want to go home in one piece.
“The key to a successful plant is that they treat each other like family,” Chris said. “Team members look out for one another. That comes from including everyone in the process and not a unilateral decision that is pushed on to everyone else.”
Prioritizing Protection with Safety Days
Covia’s Safety Day program started as a way to have the entire company united in safety at the same time – regardless of location. It allowed our team to take a step back from production to focus solely on safety for a day.
In addition to emergency preparedness, Safety Day encourages plants to focus on different elements of health and safety. For instance, one year a plant might focus on fire drills with the local fire department while the next they practice confined-space rescue drills.
For Safety Day 2024, plants ran mobile-equipment fire drills to learn about new internal policies around mobile-equipment fires. These drills help ensure that all team members are aware of what to do, how to respond, how to interact with first responders, and how to ensure everyone makes it out safely if fire were to break out.
“I remember my first Safety Day” Mona remarked. “I was absolutely impressed by everyone’s dedication to safety. I’ve never heard of a company doing this sort of thing.”
Chris added, “I like how Safety Day challenges our policies and how we would react to hypothetical scenarios. Like, what would we do if a mobile equipment operator had a heart attack? How would we rescue them? How would we get them out of their cab?”
“This is important in case a real crisis scenario was to happen,” Chris continued. “Without practicing and knowing the gaps, our response would be delayed and put people at risk.”
This is why Covia goes the extra mile to educate team members on procedures. From fire extinguisher demonstrations to a mock electrocution where an emergency helicopter was dispatched to evacuate the test person – Covia is invested in maintaining the health and well-being of all of our team members.
For further information regarding Covia's core value of Safety First and its significance in our operations, please visit CoviaCorp.com.