The Second Lives of Lithium-ion Batteries
First on the road, then at home: after serving their time in electric vehicles, recycled lithium-ion batteries make ideal stationary energy storage devices.
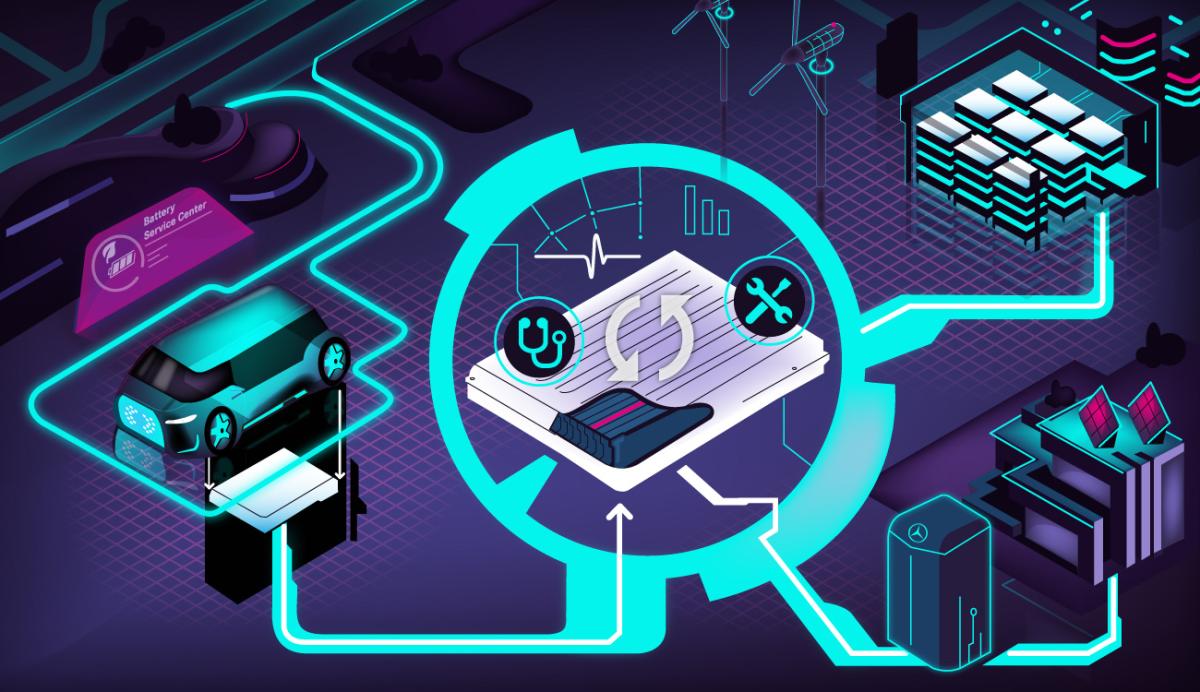
As featured on www.mercedes-benz.com | The Second Lives of Lithium-ion Batteries
Lithium-ion batteries are the untiring driving force behind electric mobility. They deliver their full output on board vehicles for at least ten years. Nevertheless, there always comes a point where a battery makes its last journey and is duly removed from service. But even after completing their automotive stint, there’s still life in these power packs. These batteries are veritable treasure troves of raw materials.
At Daimler subsidiary ACCUmotive, a rechargeable battery’s second lease of life begins to take shape well before its first active phase. Right from the earliest development stages, recycling is a prime consideration, in addition to avoiding prohibited substances such as lead and chromium VI.
Recycling and remanufacturing
In addition, “we consider right from the very early planning phase whether certain materials have proven particularly suitable for recycling purposes in the past”, notes Hartung Wilstermann, Executive Director of ACCUmotive in Nabern, where the batteries for the electrified Mercedes models are developed. In this connection, the batteries are also designed such that they can be opened easily in an expert manner and the components can be replaced easily and without any risks.
Apart from classic recycling at the end of a battery’s useful life, involving removal of its valuable materials and reprocessing for different applications, decommissioned energy accumulators can also remain in use after being duly examined. With so-called remanufacturing, the battery continues to be used after replacing defective components.
Cutting costs, protecting the environment
“This means that it is important for the battery to be designed from the outset in such a manner as to facilitate the replacement of components”, explains Wilstermann. When a battery cannot be repaired because a certain element is not replaceable, this leads to unnecessary and above all costly waste. “This can be avoided by according due consideration to remanufacturing right from the start of the development process”.
In this way, costs are reduced for customers while at the same time helping to protect the environment. ACCUmotive applies its extensive experience in the field of lithium-ion storage batteries in the development, production and recycling of batteries. “We are the battery manufacturer with the most extensive experience in this field worldwide. The first car with a lithium-ion battery was the Mercedes-Benz S400 in 2009″, Wilstermann points out.”Today, we are already in the fourth generation”.
Nickel, cobalt, copper
At the end of their service lives, the batteries are treasure troves for recycling purposes. “First and foremost, nickel, cobalt and copper are retrieved from the battery as salts”, explains chemist Barbara Seling. These metal salts are employed in the area of electroplating, for example. The slag which is additionally produced when melting down the batteries is used in road construction – so things really do come full cycle in the truest sense. The plastic is used in energy production. Battery recycling ultimately attains a recycling rate of 70 to 80 percent. “There’s probably potential for a further increase in this figure, but we are already well above the legally prescribed minimum of 50 percent”, explains Wilstermann.
Bonded, screwed, welded
The batteries are disassembled by trained electricians at specialised companies. ACCUmotive provides each recycling company with disassembly instructions for the respective battery types, which entail differences right from the opening stage of the process. “The batteries are either bonded, screwed or welded, and it is also crucial to know where the dangerous high-voltage areas are located. The batteries from the various manufacturers also differ in this respect”, explains Wilstermann, providing an idea of the challenges facing the companies which venture to tackle these complex energy storage devices.
At Mercedes-Benz the battery forms part of the vehicle’s overall concept and thus needs to be designed differently from model to model. In view of the varying installation space and the different requirements imposed on the energy accumulators, complete standardisation of the batteries, which would further simplify the disassembly process, is not possible.
Battery recycling involves experts working with high voltages, and thus calls for the very highest safety standards. A single mistake can have fatal consequences. “Protecting the developers and workers is consequently the prime priority during the development phase for a new battery, which lasts a good three years, with prototypes continually being set up and dismantled again”, notes Wilstermann. The same applies to the subsequent processing of batteries after they have completed their active service on board automobiles.
Lithium-ion batteries are the untiring driving force behind electric mobility. They deliver their full output on board vehicles for at least ten years. Nevertheless, there always comes a point where a battery makes its last journey and is duly removed from service. But even after completing their automotive stint, there’s still life in these power packs. These batteries are veritable treasure troves of raw materials.
At Daimler subsidiary ACCUmotive, a rechargeable battery’s second lease of life begins to take shape well before its first active phase. Right from the earliest development stages, recycling is a prime consideration, in addition to avoiding prohibited substances such as lead and chromium VI.
Recycling and remanufacturing
In addition, “we consider right from the very early planning phase whether certain materials have proven particularly suitable for recycling purposes in the past”, notes Hartung Wilstermann, Executive Director of ACCUmotive in Nabern, where the batteries for the electrified Mercedes models are developed. In this connection, the batteries are also designed such that they can be opened easily in an expert manner and the components can be replaced easily and without any risks.
Apart from classic recycling at the end of a battery’s useful life, involving removal of its valuable materials and reprocessing for different applications, decommissioned energy accumulators can also remain in use after being duly examined. With so-called remanufacturing, the battery continues to be used after replacing defective components.
Cutting costs, protecting the environment
“This means that it is important for the battery to be designed from the outset in such a manner as to facilitate the replacement of components”, explains Wilstermann. When a battery cannot be repaired because a certain element is not replaceable, this leads to unnecessary and above all costly waste. “This can be avoided by according due consideration to remanufacturing right from the start of the development process”.
In this way, costs are reduced for customers while at the same time helping to protect the environment. ACCUmotive applies its extensive experience in the field of lithium-ion storage batteries in the development, production and recycling of batteries. “We are the battery manufacturer with the most extensive experience in this field worldwide. The first car with a lithium-ion battery was the Mercedes-Benz S400 in 2009″, Wilstermann points out.”Today, we are already in the fourth generation”.
Nickel, cobalt, copper
At the end of their service lives, the batteries are treasure troves for recycling purposes. “First and foremost, nickel, cobalt and copper are retrieved from the battery as salts”, explains chemist Barbara Seling. These metal salts are employed in the area of electroplating, for example. The slag which is additionally produced when melting down the batteries is used in road construction – so things really do come full cycle in the truest sense. The plastic is used in energy production. Battery recycling ultimately attains a recycling rate of 70 to 80 percent. “There’s probably potential for a further increase in this figure, but we are already well above the legally prescribed minimum of 50 percent”, explains Wilstermann.
Bonded, screwed, welded
The batteries are disassembled by trained electricians at specialised companies. ACCUmotive provides each recycling company with disassembly instructions for the respective battery types, which entail differences right from the opening stage of the process. “The batteries are either bonded, screwed or welded, and it is also crucial to know where the dangerous high-voltage areas are located. The batteries from the various manufacturers also differ in this respect”, explains Wilstermann, providing an idea of the challenges facing the companies which venture to tackle these complex energy storage devices.
At Mercedes-Benz the battery forms part of the vehicle’s overall concept and thus needs to be designed differently from model to model. In view of the varying installation space and the different requirements imposed on the energy accumulators, complete standardisation of the batteries, which would further simplify the disassembly process, is not possible.
Battery recycling involves experts working with high voltages, and thus calls for the very highest safety standards. A single mistake can have fatal consequences. “Protecting the developers and workers is consequently the prime priority during the development phase for a new battery, which lasts a good three years, with prototypes continually being set up and dismantled again”, notes Wilstermann. The same applies to the subsequent processing of batteries after they have completed their active service on board automobiles.