China Keeps More Bottles in the System
China’s focus on returnable packaging highlights the advantages of a well-managed returnable bottle system.
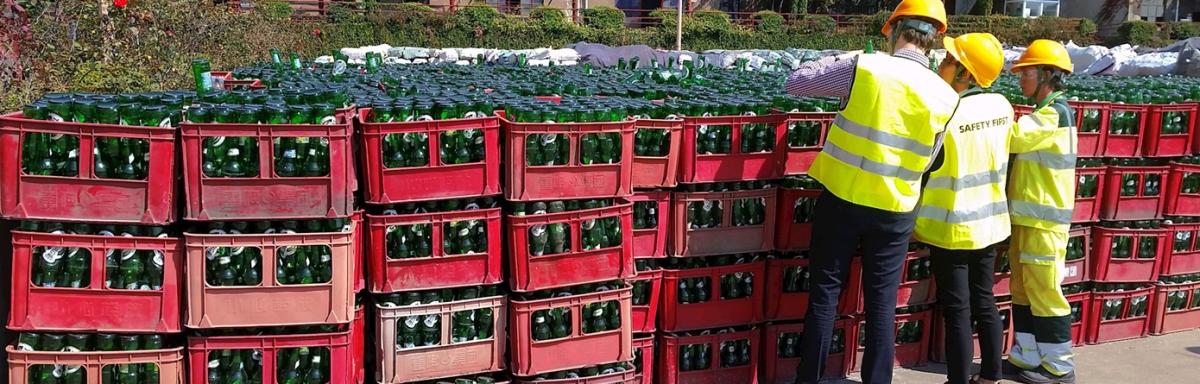
Carlsberg Case Stories | Sustainability in Action
By involving stakeholders, addressing key performance issues and implementing better return processes our Chinese operation is contributing to lower breakage rates at our own and customers’ sites.
Understanding what slows the system down
Our data collection and tracking system helps us find out which partners or customers are responsible for bottle losses or slow return times. We analyse the results to highlight the challenges that deter or prevent our stakeholders from returning bottles in a reusable state.
Supporting customers to manage issues
The challenges our customers and other stakeholders face range from deposit value in the value chain, to distance between source and consumer, to control over the return process. Once we understand a specific customer’s issues, we can offer the support as they learn to manage them.
How to get more bottles returned
Understanding the value chain is one way to get more bottles returned; another is to keep breakage rates low. China has made great strides in both these areas. They have worked with customers and bottle collectors to ensure the bottles are treated with care in the return process, for example by transporting them in crates. And they have worked with suppliers to improve the quality of bottles to limit breakages.