World Water Day 2023: A Ripple Effect
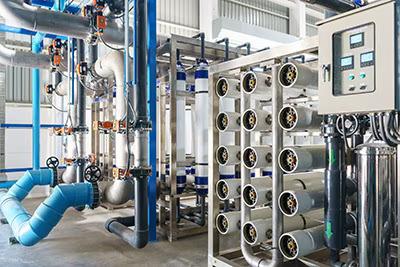
Sometimes saving water starts with a simple question: What if?
Twenty-five years ago, when reverse osmosis (RO) technology was installed at our Coatings plant in Kankakee, IL, the decision was made to not recycle the water leftover from the filtering process. Scott Bassett, who works as senior improvement manager at the plant, decided recently to take another look.
“We were looking for ways to reduce our water footprint in our community by better managing water consumption and wastewater generation,” Bassett said. “We looked at our RO process and identified a cost-effective way to fully recycle the wastewater stream.”
The result was significant: a 30% reduction in the annual wastewater generated by the plant and 14% annual reduction in water consumption. The project also saves Dow $100,000 in costs annually.
Manufacturing the coating materials that go into paints requires highly purified water. The RO unit at the Kankakee plant filters municipal drinking water to create a stream of 70% treated water, suitable for manufacturing, and a stream of 30% reject water that contains concentrates such as minerals. Previously, this reject water had been incorporated into the plant’s wastewater stream.
In search of solutions to reduce the plant’s impact on local water generation and wastewater treatment assets, Bassett and his team asked a simple question: What if the high concentration reject stream was redirected to the front of the plant and into the general water supply? That would enable the RO concentrate water to be diluted enough to be suitable for the plant’s manufacturing processes.
“We performed calculations to determine how much of the waste stream could be recycled back into the site’s general utility water supply and determined that even if 100% of the concentrate steam was recycled, the RO unit would be able to produce acceptable quality process water,” Bassett said.
Given the recycled water’s higher mineral concentration, the site’s engineering team worked with its water treatment vendor to determine the impact of the recycle stream to other utilities, such as cooling towers and boiler systems. The vendor was able to make the necessary operational and chemical changes needed to manage the recycled stream.
In addition to reducing the potable water the plant uses and cutting back on wastewater in Kankakee, the project could have positive ripple effects across Dow. It has been identified as a best practice that other facilities can potentially leverage to find similar benefits. It has also been nominated for a Sustainable Environmental Engagement at Dow (SEED) Award for its positive impact on water sustainability.
“This is what happens when you look through the lens of sustainability – a positive sustainability outcome with economic benefits,” said Jeffrey Moretti, operations sustainability manager for Coatings and Performance Monomers. “There are projects like this out there. We just have to go find them.”
Basset agrees that progress around sustainability sometimes starts with a new mindset.
“The answer is simple – the right people got engaged in the right way to find a solution for reusing water,” he said. “Now we’re more efficient at the water we take in, and our water intensity has gone down.”