Steps To Build a World-Class Health and Safety Management System
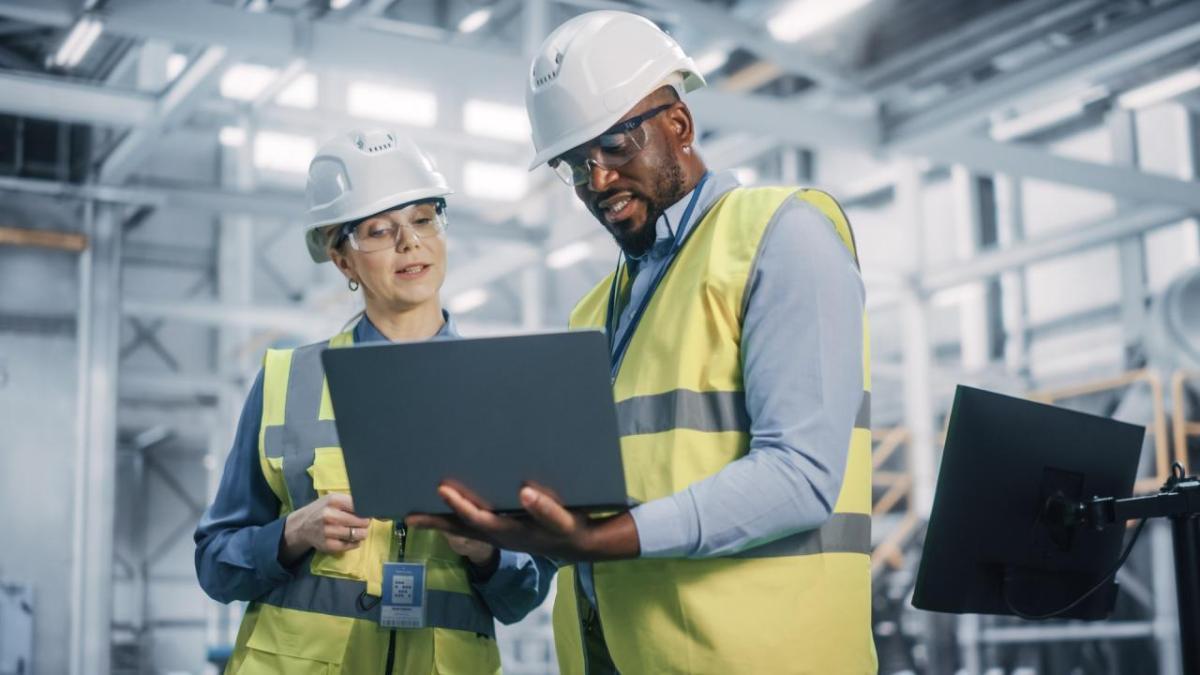
The best way to ensure the long-term safety of your workplace is to identify and mitigate potential risks before they become a problem. This is exactly what an occupational health and safety management system (OHSMS) sets out to do.
An effective OHSMS is designed to empower your entire workforce with the tools and resources they need to understand their role in implementing the OHSMS. It should also continuously improve the workplace’s safety standards while boosting morale, productivity, and work culture at the same time.
This blog offers everything you need to know to build a world-class OHSMS in your workplace.
What is a Health and Safety Management System?
An OSHMS is a formal, top-down, organization-wide approach to managing occupational health and safety risk and assuring the effectiveness of risk controls. This includes systematic procedures, practices, and policies for the management of risk. The primary goal of an OHSMS is to establish clear health and safety standards that the entire organization can follow to proactively mitigate risks. Many organizations take a custom approach to implementing an OHSMS that focuses on their individual needs while including applicable regulatory requirements. Some organizations choose to become International Standard Organization (ISO) certified. What works for one organization will likely look different from others.
Benefits of Implementing an Effective OHSMS
Promotes Safety: An OHSMS is a process for promoting health and safety while reducing risks to employees at work and by making these processes a core value.
Reduces Risk and Controls Hazards: OHSMSs require proactive hazard identification and risk management. Organizations use these systems to identify, assess, and control hazards in all aspects of their operations. An effective OHSMS prevents incidents such as injuries and process failures, and above all else, builds on the foundation of worker safety and focuses on continuous improvement. They help organizations reduce risks to acceptable levels.
Performance Management: Organizations use OHSMS to plan, set goals, and measure performance at specific intervals to determine if the management system is effective. Oftentimes, organizations that implement effective systems see increases in performance (and thus, an increase in profits) due to a decrease in incidents and losses.
Worker Engagement: An OHSMS is intended to be implemented throughout all levels of an organization, including top leadership through the lower-level or frontline workers. OHSMSs are based on leadership and overall accountability. Once the OHSMS is fully integrated in an organization, it becomes the foundation on which people perform their jobs.
Continuous Improvement: A common thread in all types of OHSMSs is the element of continuous improvement, which helps an organization identify opportunities for work and process improvements. Many OHSMSs use the Plan-Do-Check-Act approach for achieving continuous improvement.
Key Elements of a World-class Health and Safety Management System
If you want your OHSMS to be as effective as possible, it will need to contain each of the following elements:
- A definition of and commitment to organizational health and safety: First, your OHSMS should define its goal for the health and safety of your organization on your terms. You will design the system around achieving this goal.
- An accounting of all potential health and safety risks: Be as exhaustive as possible and include everything that you want your safety managers to check on during their inspections.
- Detailed instructions on all safety protocols: List and describe the safety protocols your workers need to follow on the job in detail. Your safety managers should be able to use these instructions to ensure these protocols are being followed during inspections.
- A comprehensive safety management and evaluation strategy: Lay out a step-by-step program for safety managers to follow when evaluating the current safety of your workplace, and management steps to take if their evaluations uncover problems.
- Training and awareness programs: Include a plan for training your workforce to adopt and practice any necessary safety protocols they have not already implemented. Safety training should be proactive and ongoing.
- A plan for bi-directional communication on health and safety matters: Include a system for workers to report health and safety concerns to management, as well as a way for safety managers to regularly update and inform workers on safety concerns as soon as they’re identified.
- A commitment to continuous health and safety improvement: The best OHSMS include actionable plans to continuously reevaluate and improve upon health and safety protocols. Revisit your OHSMS whenever you conduct a health and safety audit and look for ways you can continue to improve upon it.
International Standards for OHSMS Development
As you design and implement your OHSMS, below are some other examples of standards your organization can use to develop your management system. While it’s important to note that these aren’t legal requirements, they still may be useful to include for your organization.
- ISO 45001: This is the internationally recognized standard for occupational health and safety management systems. It establishes a framework for OHSMS policy, objectives, planning, implementation, operation, auditing, and review based on the “Plan-Do-Check-Act” methodology.
- ISO 14001: This establishes a framework for organizations to design and implement environmental management systems. Its objective is to help organizations find ways to minimize their carbon footprint. Many organizations can use ISO 14001 to support their overarching environmental, social, and governance (ESG) goals.
- ISO 9001: This is the world’s most well-known standard for quality management. This framework helps organizations of all sizes and sectors implement, maintain, and improve a quality management system.
- ISO 45003: This update to ISO 45001 adds guidelines for identifying and managing psychosocial workplace risks and for promoting psychological well-being at work.
- ANSI Z10: These guidelines provide OSHMS considerations and provide flexibility and guidance on how different organizations can conform.
How to Implement a Health and Safety Management System
Many effective OHSMS use the Plan-Do-Check-Act (PDCA) Approach:
The planning stage involves planning, defining controls, documenting procedures, identifying resources, and stating objectives. This stage is where the organization establishes overall objectives and processes necessary to deliver results in accordance with the OHSMS policy. What does the organization want to get out of an OHSMS and how will they get there? What resources do they have in place that will help them achieve their goals?
The do stage is when the organization takes action and implements what they outlined in the planning stage.
Check is focused on measuring the OHSMS for effectiveness and monitoring for conformity. Is the OHSMS achieving the intended goals? Is the organization implementing the procedures they said they would?
Act is the stage where the organization analyzes the effectiveness and makes changes to the management system processes as needed. The overall goal for any management system is to improve its effectiveness.
Plan-Do-Check-Act emphasizes continuous improvement.
Conclusion
Building a world-class OHSMS isn’t easy, but the results are well worth the effort. If you’d like professional support and guidance creating a fully compliant and effective OHSMS, reach out to Antea Group’s EHS Management System Support experts to discuss how we can support your organization along your OHSMS journey.
Antea Group has also created A Practical and Tactical Guide to Top-Down EHS Management that may help you in your implementation.