SEE Global Impact Report: Achieving Zero Harm
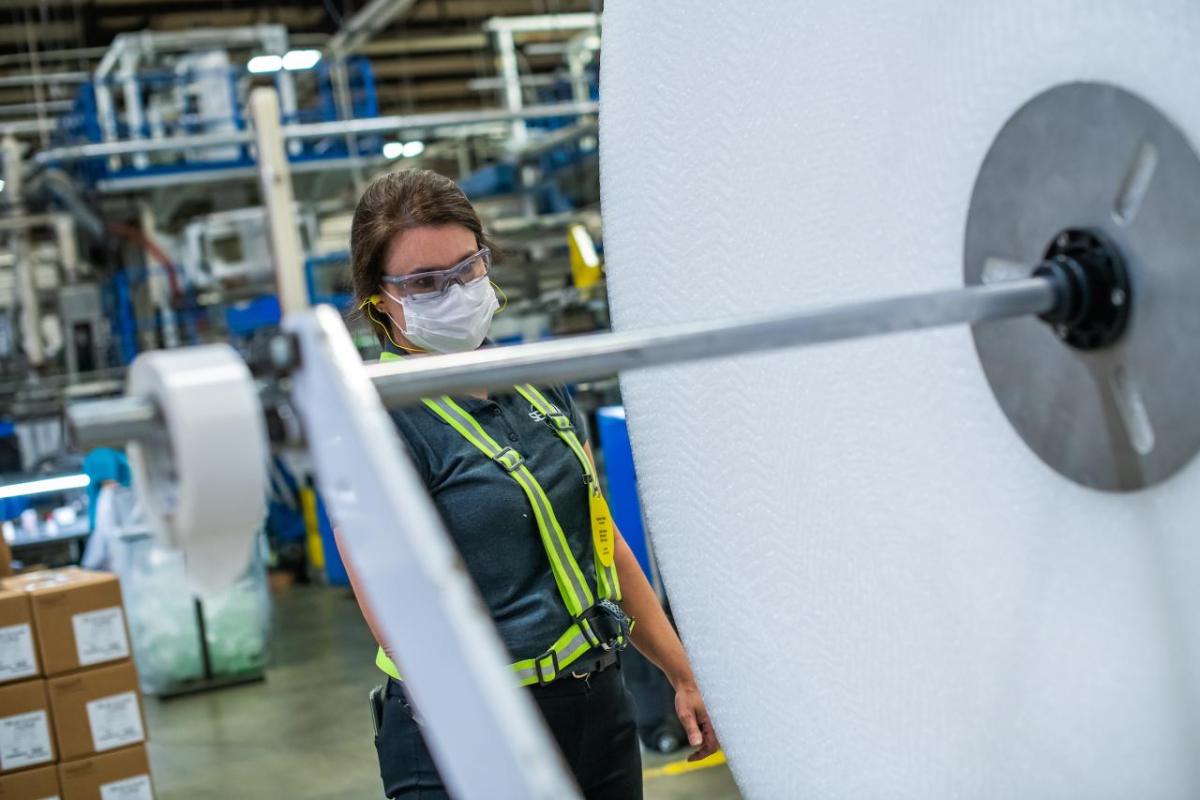
Originally published in SEE's Global Impact Report
SEE® (formerly Sealed Air) is creating an overall culture of health, safety, and well-being for our people. As a manufacturing company, protecting the health, safety and well-being of our people is critical. Our goal is to be free of accidents with zero harm, and we have structured our operations to provide employees with a safe and healthy working environment.
SEE’s Zero-Harm Performance for 2021
- Total recordable injuries reduced by 8%
- 64% of SEE manufacturing plants achieved zero recordable incidents in 2021
Environmental, Health and Safety Policy
SEE’s Environmental, Health and Safety (EHS) policy outlines the company’s commitment to integrate EHS principles in all aspects of the business, including products, operations, and supply chain.
The policy requires SEE’s employees and contractors to conduct business in accordance with applicable environmental, health and safety laws and understand and comply with company procedures and guidelines to protect the environment, health and safety of themselves and their co-workers.
The policy includes SEE’s commitment to:
- Provide training programs for employees to perform their jobs safely and in an environmentally responsible manner, and to understand their role in complying with policies, procedures and guidelines
- Focus on the design and development of products that enable customers to reach their EHS goals by reducing waste, increasing operational efficiency, protecting human health, and improving food safety and security
- Conserve raw materials, water and energy in our operations through source reduction, process improvement, use of alternative materials, and waste recovery
- Actively pursue programs to reduce the overall GHG intensity of our operations
- Share our EHS policy with customers, suppliers, shareholders, and the local communities in which we operate, where applicable
- Establish targets and be transparent in reporting publicly on our progress towards improving our EHS performance
- Develop sustainable solutions that make our world better than we find it
Health and Safety Audits
Health and safety audits are conducted at each of SEE’s manufacturing sites minimally every three years by teams comprised of local, regional and global resources. In 2021, 28 health and safety audits were conducted. In addition to the audits, machine risk assessments based on ISO standards, have been administered throughout our operations with support from external safety consultants.
EHS standards are reviewed minimally on an annual basis to verify relevance and completeness and to identify opportunities for improvement. The EHS standards are updated as part of an ongoing continuous improvement process in response to changing regulation and audit finding trends. Every SEE facility is required to implement the relevant elements of the company’s EHS standards. The Audit Committee of SEE’s Board of Directors regularly reviews EHS matters.
Investing in Safety
SEE’s commitment to safety includes capital investments that improve the safety of our existing equipment and the design of new machines. Early in the design process, our global engineering team conducts risk assessments in accordance with ISO standards to ensure that all machines function to the highest safety standards.
Training Programs
SEE’s global EHS program includes behavioral-based safety training, hazard identification and risk assessment, and several other preventive trainings. In addition to on-site training, in 2021 SEE implemented an online safety training program that includes topics such as lockout and tagout, machine safety, arm’s length, hand and power tool safety, and job hazard analysis. More than 19,000* training sessions were completed in 2021 achieving 94% overall completion rate for targeted employees.
*Some employees attended more than one topic training.
Emergency Preparedness Procedures
SEE sites are required to establish, implement, and maintain procedures to identify the potential for emergency situations, choose the methods for responding to those situations, and periodically test the emergency response plan.
Operation Clean Sweep
SEE is a signatory of Operation Clean Sweep®, an international program designed to prevent the release of plastic granules into the environment and water streams. By signing the Operation Clean Sweep pledge, SEE recognizes the importance of preventing spillages into the environment and commits to the following six actions:
- Improve worksite set-up to prevent and address spills
- Create and publish internal procedures to achieve zero industrial plastic material loss
- Provide employee training and accountability for spill prevention, containment, clean-up, and disposal
- Audit performance regularly
- Comply with all applicable state and local regulations governing industrial plastics containment
- Encourage partners (contractors, transporters, distributors, and others) to pursue the same goals
COVID-19
Throughout the COVID-19 crisis, SEE has followed the recommendations and guidance of health authorities and local governments across the globe. The company instituted precautionary measures for employees at all its facilities worldwide, including enhanced cleaning procedures, quarantine and testing protocols, temperature checks, face masks, engineered social distancing, remote work arrangements for non-location-dependent employees, restricted visitor access, and travel limitations.
Read Sealed Air's Global Impact Report here.
Learn More About Sealed Air’s ESG efforts here.