Safety — of Both End-Product & Personnel — is Paramount in e-Mobility and Renewable Energy Ecosystems
By Michele Robinson-Pontbriand | Director Corporate Social Responsibility
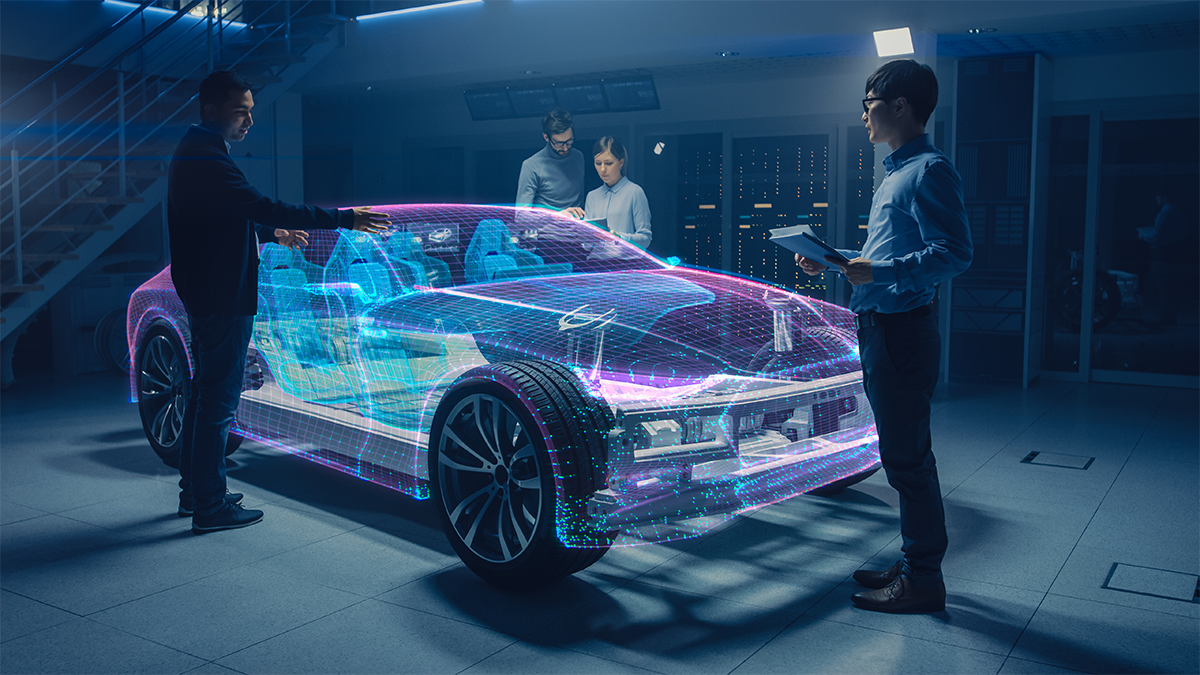
The International Energy Agency (IEA) forecasts the number of pure electric vehicles (EVs) and hybrid electric vehicles (HEVs) on the world’s roads will hit 250 million by 2030. That is a big leap from the IEA’s 5.1 million reported for such vehicles in 2018. This growth in the plug-in vehicle market is, in turn, fueling new technologies in the adjacent renewable energy ecosystem to enable mass EV/HEV adoption. These adjacent technologies include photovoltaic (PV) inverters for energy efficiency and smart grid technologies that support a network of recharging facilities.
This is great news for the environment as the e-mobility and renewable energy ecosystems will support a more sustainable future. It is also good news for the automotive and energy industries, providing new business and innovation opportunities. However, challenges abound for manufacturers in these areas. Of particular concern in this drive to the future-state is safety — both of end-products as well as personnel — throughout design and manufacturing. Quality electronic design and test solutions are key to not only help engineers verify the quality and safety of each design from development through high-volume production, but also in keeping them safe during the process.
End-Product & Personnel Safety
Throughout design and manufacturing, end-product safety is of paramount concern to manufacturers delivering e-mobility and renewable energy solutions. To that end, engineers work to simulate a vast array of real-world operational and environmental influences to evaluate both whole-system operations and safety aspects of their products.
At the same time, engineers need to use caution for their own personal safety throughout the design and manufacturing process in this high-power environment. For example, testing new semiconductors used in EV/HEV converters requires extra validation and reliability testing under harsh operating conditions. The extreme high-voltage levels used with these converters require special safety mechanisms to be in place, including redundant relay systems that do not expose personnel and equipment to high voltages if a failure occurs.
Electronic Design & Test Solutions Help Mitigate Safety Risks
To address emerging design and test issues, Keysight has created innovative approaches to help developers and manufacturers accelerate their programs while supporting personnel and end-product safety. For example, the company’s electric powertrain testing solutions ensure energy efficiency throughout different segments of the ecosystem. Engineers can use design and test tools to optimize power at the power semiconductor level, through inverter and DC-to-DC converter testing for onboard systems, as well as cell characterization and power efficiency tests for battery modules, and packs to support end-product safety. This solution does all this while also supporting engineering personnel safety through the process.
In addition, Keysight’s energy ecosystem testing solutions use leading-edge emulation technology and software, spanning solar cell testing to PV inverter efficiency testing. These help manufacturers meet stringent industry standards for safety and performance of the end-product.
While testing may seem like a small part of the full end-to-end EV/HEV delivery and infrastructure model, it is critical in safely delivering the promise of a more sustainable future through the e-mobility and renewable energy ecosystems.