Reflections on 10 Years in Bangladesh
Interview with SAI Lead Trainer Badri Gulur on his perspective of social compliance in Bangladesh from 2003-2013
Jul 23, 2013 2:00 PM ET
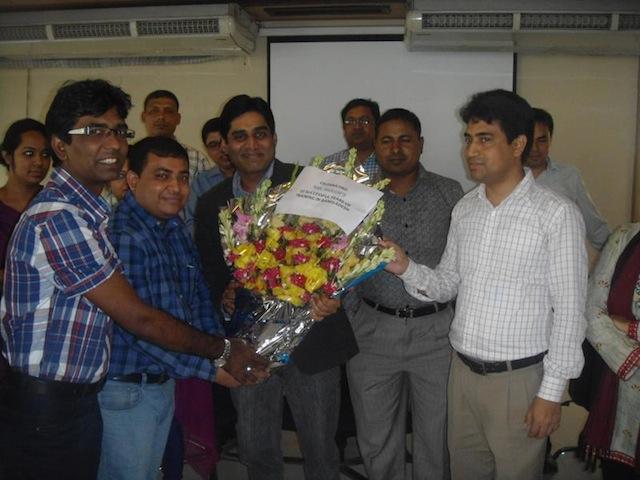
Read the article on SAI's website
Joleen Ong: You've been working with SAI for a long time doing SA8000 auditor and advance auditor training and more - when did you first start training in Bangladesh?
Badri Gulur: The first SA8000 Basic Auditor training course that I led was in June 2003. Prior to that I worked with Bureau Veritas as Country Manager for SA 8000 and certified the first factory to SA8000 in Bangladesh in 2001.
JO: After 10 years of training in Bangladesh, what are some of the broader changes that you've observed in the garment sector? BG: In general, the whole compliance bandwidth has changed. This has been both positive and negative. Ten years ago, a key focus of factories was leveraging the quota, and staying in compliance was mainly on the surface. But over the years, thanks to a lot of capacity building from our training, the concept of social compliance has moved from a 'reactive to proactive' approach. Wage discrimination towards women has declined since 2006 and they are paid at par with male workers.
With the recent media attention on Bangladesh, I've observed a lot of immediate knee-jerk reactions. For example, after the Rana Plaza tragedy, I received many queries from brands about structural stability testing and soil sample analysis. Prior to that with Tazreen and other factory fires, the focus was on fire safety risks assessments. But it's important to remember that while there may seem to be immediate responses, they must be reinforced with legal compliance and periodic monitoring.
From a workers perspective, things have not changed too much. From 1,200 BDT per month in 2001 to 1,662 BDT in 2006, wages rose to 3,000 BDT in 2010. In 2010, I spent a day with a Bangladeshi garment worker to see how much money he spends on food - it was about 60 BDT for one day. If the average monthly pay for garment workers is around 3,000 BDT (USD 37.00) Takas, then how can he make two ends meet? He will of course be reliant on excessive overtime.
On the positive side, for women garment workers, they are regarded as the lifeline of the industry. This has given them good leverage to negotiate benefits such as maternity leave and they are paid at par with male workers. Also, in the past ten years, there have been major improvements made in factories to reduce child labor. In my opinion, a lot of such improvements can be attributed to the intervention of brands, where they took a strong position against such issues and monitored through increased audits.
JO: In Bangladesh, there are only 6 SA8000 certified facilities. Can you explain why there is an interest in learning about SA8000 there? BG: I believe that many people are here because there has been a huge growth in other certification schemes in Bangladesh in the past 3-4 years. While a lot of people may not intend to go through the certification process, they are interested in learning about the management systems approach, which is information that is applicable to most schemes. No other standard talks about the relationship between performance criteria and a broad platform to ensure their implementation, the 'management system.' We have had participants taking the course in order to prepare them to work for other initiatives such as WRAP, GSCP and ETI.
In my ten years of training in Bangladesh, I've been happy to note that the course delegates have moved on to positions such as the current Bangladesh Foreign Secretary to Sweden, the District Magistrate of Dhaka and Senior compliance managers of several brands. This training helps them look at things from a practical and holistic approach to be integrated in their work and appreciate the role of management systems. To this end, I should mention my mentor Doug De Ruisseau, with whom I have co-trained, and learned a lot from his perspective.
These courses also help factory managers to get a sense of how to properly interpret the SA8000 Standard, as there can be a lot of misinterpretation out there. These courses clarify understanding of expectations and also the intent of the standard - this helps as some lose hope before they even think of pursuing certification. But an important thing that we try to teach is how a lot of things are integrated. For example, many companies in Bangladesh feel as if it is difficult to comply with the remuneration element of the standard - but the reason behind not being able to comply with that element is because they are not in compliance with working hours and there is excessive overtime. The punch line with SA8000 is 'workers should work to live and NOT live to work'. JO: What's an interesting labor trend that you've noticed in Bangladesh? BG: In Bangladesh, due to the lower wages, the large scale migration to other countries has resulted in a shortage of skilled resources in the garment industry. Companies have realized now that worker retention is crucial, especially as skilled garment workers are also sought after by recruiters from Mauritius or Middle Eastern countries, such as Bahrain, Jordan and UAE. Many companies, although not paying a living wage, try to compensate with benefits such as free transportation, free hygienic food and health insurance. The Bangladeshi workers have the record of being very hard working and productive and they want to be remunerated at a living wage. It is high time for this to become a reality in Bangladesh, which is the 2nd largest exporter of garments in the world.
JO: What changes, if any, have you seen in Bangladesh since the widely-publicized Rana Plaza tragedy? BG: Building and fire safety is taken with a lot of seriousness. There has been an increase in inspections by the government to ensure worker safety.
When I was in Dhaka, there was a building in Savar (an industrial suburb of Dhaka) that housed 5 garment factories where an inspector noticed structural cracks. The building was shut down for 3 days while a full investigation took place. Prior to Rana Plaza, it would have been a lot more difficult to halt production of 5 factories for something like this. People are reflecting back, and getting more inspections done. Also, companies are extremely uneasy about this and are being extra vigilant. After the Tazreen fire, the Dept. of Factory Inspection along with fire Service identified a total of 943 non-compliant ready-made garment units, among the nearly 3,000 factories that were visited. The same is being done with building safety after the Rana Plaza tragedy.
JO: Regarding the recent news about the US suspending trade privileges with Bangladesh - what is the overall sentiment in Bangladesh?
Badri Gulur: The first SA8000 Basic Auditor training course that I led was in June 2003. Prior to that I worked with Bureau Veritas as Country Manager for SA 8000 and certified the first factory to SA8000 in Bangladesh in 2001.
JO: After 10 years of training in Bangladesh, what are some of the broader changes that you've observed in the garment sector? BG: In general, the whole compliance bandwidth has changed. This has been both positive and negative. Ten years ago, a key focus of factories was leveraging the quota, and staying in compliance was mainly on the surface. But over the years, thanks to a lot of capacity building from our training, the concept of social compliance has moved from a 'reactive to proactive' approach. Wage discrimination towards women has declined since 2006 and they are paid at par with male workers.
With the recent media attention on Bangladesh, I've observed a lot of immediate knee-jerk reactions. For example, after the Rana Plaza tragedy, I received many queries from brands about structural stability testing and soil sample analysis. Prior to that with Tazreen and other factory fires, the focus was on fire safety risks assessments. But it's important to remember that while there may seem to be immediate responses, they must be reinforced with legal compliance and periodic monitoring.
From a workers perspective, things have not changed too much. From 1,200 BDT per month in 2001 to 1,662 BDT in 2006, wages rose to 3,000 BDT in 2010. In 2010, I spent a day with a Bangladeshi garment worker to see how much money he spends on food - it was about 60 BDT for one day. If the average monthly pay for garment workers is around 3,000 BDT (USD 37.00) Takas, then how can he make two ends meet? He will of course be reliant on excessive overtime.
On the positive side, for women garment workers, they are regarded as the lifeline of the industry. This has given them good leverage to negotiate benefits such as maternity leave and they are paid at par with male workers. Also, in the past ten years, there have been major improvements made in factories to reduce child labor. In my opinion, a lot of such improvements can be attributed to the intervention of brands, where they took a strong position against such issues and monitored through increased audits.
JO: In Bangladesh, there are only 6 SA8000 certified facilities. Can you explain why there is an interest in learning about SA8000 there? BG: I believe that many people are here because there has been a huge growth in other certification schemes in Bangladesh in the past 3-4 years. While a lot of people may not intend to go through the certification process, they are interested in learning about the management systems approach, which is information that is applicable to most schemes. No other standard talks about the relationship between performance criteria and a broad platform to ensure their implementation, the 'management system.' We have had participants taking the course in order to prepare them to work for other initiatives such as WRAP, GSCP and ETI.
In my ten years of training in Bangladesh, I've been happy to note that the course delegates have moved on to positions such as the current Bangladesh Foreign Secretary to Sweden, the District Magistrate of Dhaka and Senior compliance managers of several brands. This training helps them look at things from a practical and holistic approach to be integrated in their work and appreciate the role of management systems. To this end, I should mention my mentor Doug De Ruisseau, with whom I have co-trained, and learned a lot from his perspective.
These courses also help factory managers to get a sense of how to properly interpret the SA8000 Standard, as there can be a lot of misinterpretation out there. These courses clarify understanding of expectations and also the intent of the standard - this helps as some lose hope before they even think of pursuing certification. But an important thing that we try to teach is how a lot of things are integrated. For example, many companies in Bangladesh feel as if it is difficult to comply with the remuneration element of the standard - but the reason behind not being able to comply with that element is because they are not in compliance with working hours and there is excessive overtime. The punch line with SA8000 is 'workers should work to live and NOT live to work'. JO: What's an interesting labor trend that you've noticed in Bangladesh? BG: In Bangladesh, due to the lower wages, the large scale migration to other countries has resulted in a shortage of skilled resources in the garment industry. Companies have realized now that worker retention is crucial, especially as skilled garment workers are also sought after by recruiters from Mauritius or Middle Eastern countries, such as Bahrain, Jordan and UAE. Many companies, although not paying a living wage, try to compensate with benefits such as free transportation, free hygienic food and health insurance. The Bangladeshi workers have the record of being very hard working and productive and they want to be remunerated at a living wage. It is high time for this to become a reality in Bangladesh, which is the 2nd largest exporter of garments in the world.
JO: What changes, if any, have you seen in Bangladesh since the widely-publicized Rana Plaza tragedy? BG: Building and fire safety is taken with a lot of seriousness. There has been an increase in inspections by the government to ensure worker safety.
When I was in Dhaka, there was a building in Savar (an industrial suburb of Dhaka) that housed 5 garment factories where an inspector noticed structural cracks. The building was shut down for 3 days while a full investigation took place. Prior to Rana Plaza, it would have been a lot more difficult to halt production of 5 factories for something like this. People are reflecting back, and getting more inspections done. Also, companies are extremely uneasy about this and are being extra vigilant. After the Tazreen fire, the Dept. of Factory Inspection along with fire Service identified a total of 943 non-compliant ready-made garment units, among the nearly 3,000 factories that were visited. The same is being done with building safety after the Rana Plaza tragedy.
JO: Regarding the recent news about the US suspending trade privileges with Bangladesh - what is the overall sentiment in Bangladesh?
BG: When the news broke in Dhaka, many of the newspapers seemed to project that it was a political decision, one that was too knee jerk from the US. Since the EU did not suspend trade privileges through the GSP (Generalized System of Preferences), they believe that this decision was linked with the fact that most American companies did not sign on to the Bangladesh Safety Accord.
But overall, it's a mixed bag. The most interesting thing I heard someone say in Bangladesh was - "why blame the GSP? We always react when something has been suspended, but has the Bangladesh government actually done anything in terms of worker safety and welfare for the last 10 years?" To sum it up, social compliance is a journey and needs the right spirit and intent. As my SAI colleague Craig Moss puts it, 'employers need to think from the 'heart' and not just from the 'head'.