Maximizing the Potential of Smarter, Better, Circular Strategies
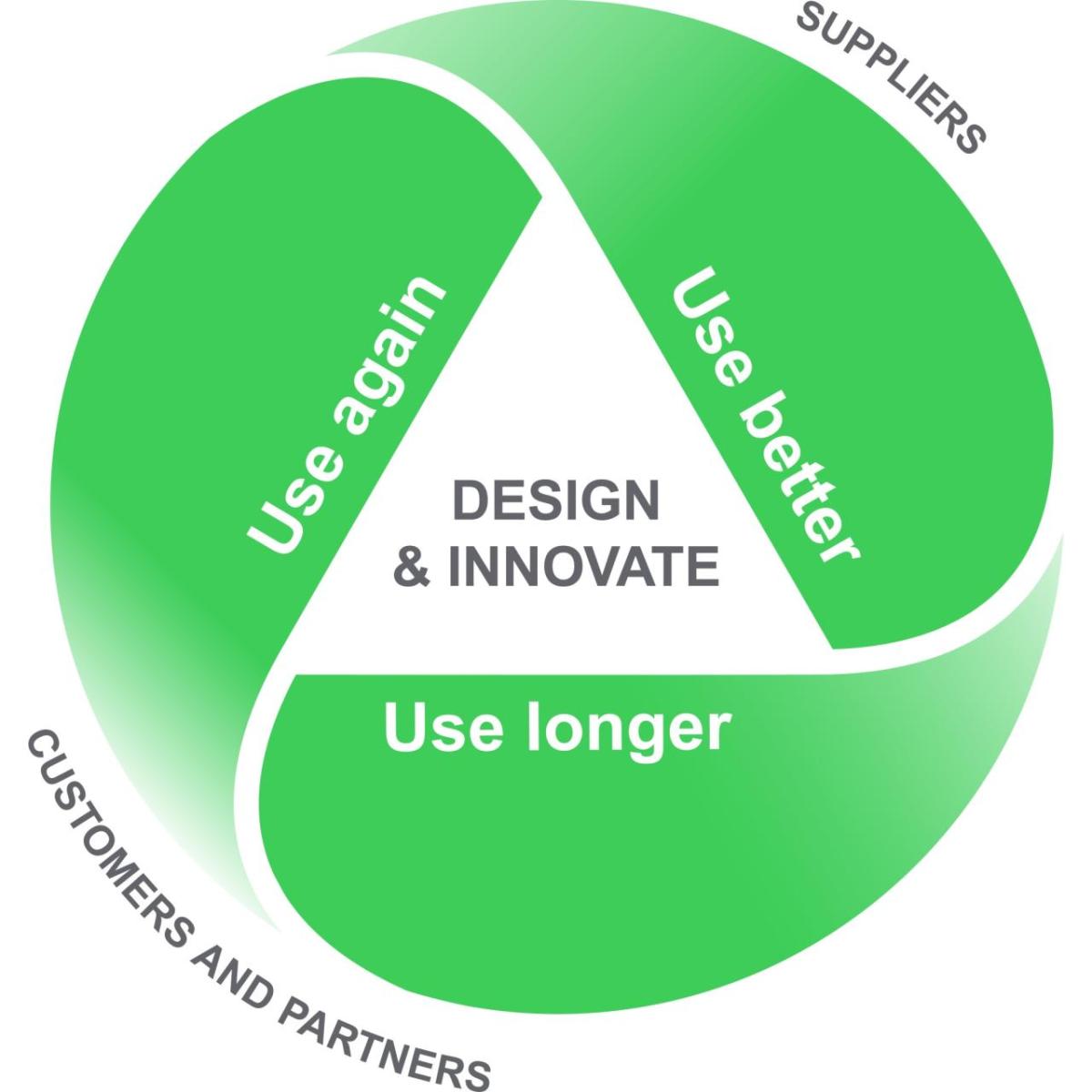
Circularity is the philosophy and practice of using less, using better, using longer, and using again — preserving resources to extract the maximum value from them. It is not only common sense, but good business sense too.
A sea of unrealized opportunities
Every year, vast amounts of waste wash up on coastlines, a heavy burden for our planet, and a symbol of unrealized efficiencies.
Our global circularity rate is declining. According to the Global Circularity Gap report 2024, while material consumption kept increasing, the share of secondary materials used worldwide decreased significantly from 9.1% in 2018 to 7.2% in 2023.
Consider the scale of lost opportunity: circularity alone could mitigate nearly 75% and 60% of CO2 emissions of the built environment and transportation sectors respectively by 2050. And with an estimated 7% potential increase in GDP by 2030, the circular economy is more than environmentally sound, it is a growth line. From the EU’s Circular Economy Action Plan to the US National Recycling Strategy, policies and incentives already exist as a framework.
Transitions like the regionalization of supply chains are also implementing circular practices like better sourcing, smarter production, and more refurbishing, recycling, and reparability. This is welcome news, because given the urgent context, we must realize the potential of circularity. It holds the key to transforming our businesses into catalysts for efficiency, resilience, and sustainable value propositions.
From systematic to systemic change
Like all programs that reduce environmental footprints, circular transitions require a systematic approach: initiatives underlined by measurable and complementary targets, driven by both internal and external stakeholders.
Not only that, but the systemic nature of circularity also means changing more than linear approaches. It also necessitates an ‘everywhere all at once’ transformation across all aspects of consumption and production. This process has four phases: Design & Innovate, Use better, Use longer, and Use again — and requires a coordinated shift in mindset.
These requirements underpin Schneider Electric’s own transformation journey.
Smarter, better, more circular
At the heart of a circular transformation lies the ‘Design & innovate’ phase, affecting product development and innovation. This phase plays a pivotal role in maximizing value retention, influencing up to 80% of a product’s lifecycle impact. At Schneider Electric, we regularly revitalize and redeploy our EcoDesign tools and training. These support teams like R&D deliver more value from extra reliability and longer life and develop new as-a-Service solutions.
The ‘Use better’ phase is about sourcing materials and manufacturing products as sustainably as possible, with minimal waste. For example, using better procurement strategies, we went from 7% sustainable material content in 2021 to 29% in 2023, with the aim of reaching 50% in 2025. Similarly, we rose from 13% to 63% use of sustainable packaging in the same period, with the goal of reaching 100% primary and secondary packaging by 2025, free from single-use plastic.
Beyond using recycled materials and renewable energy, smart factory operations — like digitized shopfloor, connected machines, and data and analytics — also contribute to circularity by creating new forms of efficiency and flexibility. For example, over four years, our Hyderabad plant reduced its energy consumption by 59%, water consumption by 57%, CO2 emissions by 61%, while improving waste optimization by 64%. It was recognized as a “Sustainability Lighthouse” by the World Economic Forum in 2023.
The ‘Use longer’ stage helps extend the lifespan of products to delay the need for new ones. It involves condition-based repair and digitally enabled maintenance and equipment modernization services. For instance, we chose to launch a set of ECOFITtm retrofit services to facilitate equipment upgrades by replacing certain key components, rather than the entire system.
Finally, the ‘Use again’ phase covers the recirculation of products, parts, and materials in the economy. That includes refurbishing and reselling assets that are reaching their end of use. With our refurbishing and repackaging program pilot in France, we use digital tracing and reverse logistics for the end-of-use stage. Once a product is recollected at Schneider Electric, we evaluate whether to repair, reuse, refurbish, or recycle. We also include all relevant information when returning the product to the market, including performance. This is how we have avoided over 300,000 tons of primary resource consumption since 2017.
While each step plays a crucial role, it is vital to understand the natural hierarchy within this approach. The cost to recover value tends to increase as the product lifecycle progresses. For example, it is much more efficient to optimize the use of raw material in the design phase (‘Use better’) than to recover raw material from products at the end of their use (‘Use again’). This is how to best maximize value retention throughout the asset lifecycle.
Charting the path
At Schneider Electric, our commitment to circularity began over two decades ago and continues to the present day. With a focus on sustainable innovation and a close collaboration with the Ellen MacArthur Foundation in 2015, our aim is still to bring the concept of circularity from theory to the core of our business.
While we have seen that the journey is not always straightforward, it must be smarter, better, and more circular. And this can only be achieved together.