Managing Supply Chain Disruptions in the Pharmaceutical Industry
by Niranjan Kulkarni, PhD Director of Operations Improvement
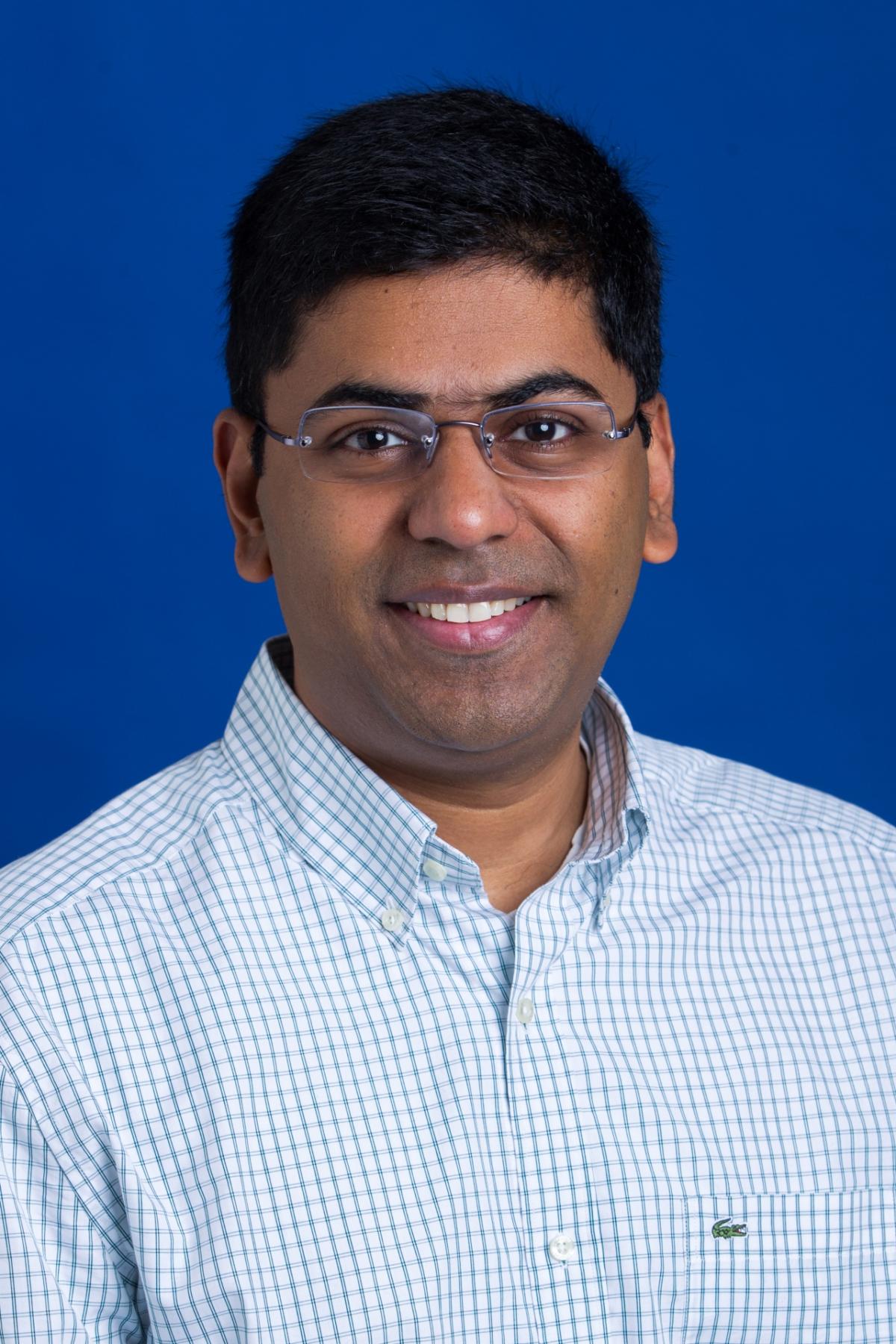
The COVID-19 pandemic will have far-reaching implications, including supply chain disruptions for pharmaceutical manufacturers.
Rightly so, most of the concern is currently on finding a vaccine and creating the process and facilities to manufacture it quickly, at-scale. But there is also the possibility that many people the world over may have difficulty getting other essential medicines because resources (time, materials, equipment, etc.) will be diverted to the manufacture of an eventual vaccine. Furthermore, the bulk of critical ingredients and raw materials used to manufacture medications and devices are made in China. The U.S. Food and Drug Administration’s Center for Drug Evaluation and Research reports that about 14% of the facilities that make active pharmaceutical ingredients (API) are in China. China also ranks second among countries exporting drugs and biotech medicines to the United States. Though drug shortages are not common yet, there are some reports tying the deadly outbreak to its first drug shortage event. These events are going to test the pharmaceutical supply chain’s robustness and resiliency, as it highlights some glaring weaknesses.
In general, rare events, like the coronavirus pandemic, can create some of the following challenges to supply chains:
- Reluctance to receive raw materials/products from an impacted geographical location
- Sourcing issues, e.g. single source supply—especially damaging if the supply source is impacted and unable to satisfy demands
- Site(s) closure impacting production capabilities
- Transportation issues/disruptions
- Introduction of counterfeit material in the supply chain
- Lack of coordination and traceability in supply chain causing either significant build-up or shortage of inventory (bullwhip effect)
Solely relying on digital (information technology) solutions may not be adequate. Pharmaceutical manufacturers should also evaluate operational strategies to mitigate or minimize disruption impact.
Operational strategies to overcome supply chain disruptions include:
- Adopting multi-sourcing strategies, e.g. having a Tier 1 and a qualified Tier 2 supplier for the same material
- Allocating demands to or increasing capacities of other site(s)
- Evaluating alternate distribution channels and methods
- Managing safety stock by evaluating severity (length) and the likelihood of disruptions
- Sharing information in supply chains, investing in supplier development and collaboration with competitors
Multi-site sourcing and demand allocation:
Consider sourcing raw materials from multiple suppliers or working with one supplier that has manufacturing capabilities at multiple locations to reduce overall sourcing disruption risks. Using the same philosophy, also evaluate how to allocate production across multiple facilities, either within your own network or outsourcing to contract manufacturing organizations (CMOs). It is crucial for pharmaceutical manufacturers to continuously evaluate sourcing strategies in terms of site capabilities, risk profile, cost and any additional sourcing complexities.
To understand your network’s readiness to adapt to these changes, perform a gap/risk analysis using strategic facility planning (SFP) methods. SFP compares facility capacities (supply) to business needs (demands). It allows you to identify gaps and risks and perform scenario analysis. Complete this for every node within the supply chain network.
Contingency planning and efficiency improvement
Supply diversification has direct, and indirect costs associated with it. As a temporary stop-gap solution, you can use a supplier, or a production site not normally used to keep operations running. Generally, this strategy works for short-term disruptions. However, in the case of long-term disruptions, this can be cost-prohibitive. In either case, raw material or production pricing will be impacted. Thus, it is prudent to become cost-effective and lean by reducing inefficiencies in production processes, while improving the use of available (and in some cases more expensive) resources. Increasing operational efficiency, which should be a normal work-day goal, becomes even more important in days of a crisis, i.e., prolonged supply disruption.
Managing safety stock
Increasing safety stock can look like a straight-forward solution to mitigate risk. However, it can become significantly expensive and ineffective, especially when disruptions are longer than anticipated. To find the right safety stock balance, implement an adaptive inventory strategy. Adaptive inventory strategy pairs your risk profile based on severity and occurrence with ongoing detection of potential threats to supply continuity. This informs the realignment or adjustment of your existing inventory strategy. In the case of perishable goods inventory, additional variables come into play, making the detection and severity ranking even more complex.
Furthermore, estimating the right quantities of safety stock can be challenging. A special case of Monte Carlo simulations, i.e., Discrete Event Simulations (DES) can be used to overcome this challenge. DES has the capability to model uncertainty and variables inherent in process times, and perform ‘what-if’ analysis.
Supplier development and information sharing
A crucial part of your relationships with suppliers is collaboration, paired with commitment in business agreements. Get involved directly with your suppliers for improvement efforts to reduce supplier induced disruptions. A few ways you can mitigate your risk include frequent onsite audits, increased inspections and increased supplier training. Improved communications can help pharmaceutical companies react to upstream disruptions and tackle demand management by either switching to non-constrained products or rationing.
Mathematical and financial modeling techniques are well suited to evaluate new sourcing strategies, to assess the cost associated with qualifying new suppliers and to solve demand allocation problems. DES can further provide insights into multi-node complex supply chains, where disruptions can occur at any stage. These techniques can help conduct stress tests for pharmaceutical supply chains by performing scenario analysis. We’ve used these simulations with clients to effectively prepare them for worst-case scenarios and in developing their strategic response plan.
However, these analyses are performed at a macro level and they may not adequately capture the impact on facility operations. Evaluating operational impacts requires modeling supply chain and manufacturing processes together. DES models can be developed to quantify the impact on work-in-progress, lead times, campaign scheduling, etc. which subsequently influence the cost of goods and responsiveness.
Responding to supply chain disruptions is most effective when done proactively. While all strategic plans will face some level of inaccuracy or fall-outs, pharmaceutical companies should constantly strive to find the best strategy that works for them. There is no ‘one size fits all’ solution to disruption management. In order to find which strategy works best, look at your existing business processes, as well as operational and compliance requirements.
At the operational level, pharmaceutical companies should prepare for supply disruptions by:
- Always having efficient operations, including optimized usage of available raw materials and resources
- Having a robust business process to determine and strengthen weak links in their production and supply chains
- Making their strategic plan a living document with constant feedback from current events, derived insights from simulations
Questions about ways to mitigate or manage supply chain disruptions?
Contact us.