Less Is More: Building a Circular and Sustainable Economy at Gildan
Q&A with Israel David Salinas, SVP of Global Supply Chain and Production Innovation
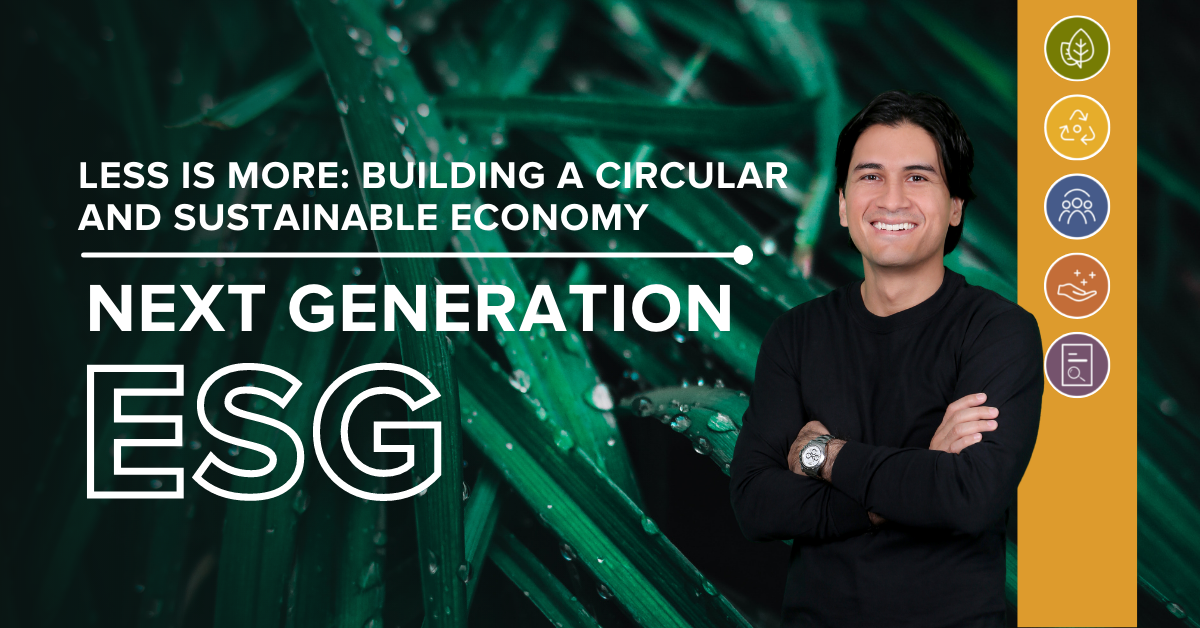
As part of its Next Generation ESG strategy, Gildan has brought forth an enhanced focus on circularity. Previously embedded within its environmental pillar, Gildan has now made it a stand-alone area in its strategy and future targets, demonstrating the Company’s enhanced commitment to circularity.
We sat down with Israel David Salinas, Senior Vice President of Global Supply Chain and Product Innovation at Gildan to hear more about the future of circularity at the Company.
With over nineteen years at the organization, Israel has led many of the Company’s efforts to innovate and use creative solutions within its manufacturing operations and to continuously find new ways to do more with less. Read on as Israel takes you behind-the-scenes of circularity at Gildan.
Why did Gildan decide to make circularity a stand-alone area of focus in its new ESG strategy?
The concept of circularity has long been an important part of Gildan’s approach to manufacturing products sustainably. Over the years, the term has changed, but the concept has remained the same: to extend the life cycle of resources.
As we were defining our Next Generation ESG strategy in 2021, circularity was already playing an important role within our environmental area of focus but based on the results from our third materiality assessment, we saw a more important need and demand to take a deeper dive into incorporating circularity within our ESG program.
Following this assessment, the decision was made to give circularity even more real estate within our go-forward plan, and from there, it became a stand-alone area of focus with its own set of future targets.
Can you tell us more about Gildan’s current efforts to promote circularity?
What I love about Gildan and our teams is that we’ve always been good at creatively challenging ourselves in different aspects of our operations to continuously find ways to do more with less.
Take for instance our biomass system, where we burn manufacturing waste – like yarn cones, palettes, and boxes – to create steam required to run our textile facilities. This is a renewable energy source, which has helped us generate roughly 40% of our total energy on average over the past five years. This process is carbon neutral because it prevents organic materials from entering landfills where greenhouse gases would otherwise be emitted during the decomposition phase. So, we’re sending less waste to landfills and we’re using that waste to generate renewable energy. A win-win situation for the planet and for Gildan!
As part of Gildan’s Next Generation ESG strategy, what exciting goals related to circularity has the Company set out to accomplish?
We are committed to fostering a circular economy to reduce our environmental impact on the planet. On top of our overall mindful consumption of the earth’s resources, we are looking for ways to use more sustainable raw materials. Here are our four goals on the circularity front:
- 100% sustainable cotton by 2025
- 30% recycled polyester or alternative fibres/yarns by 2027
- Zero manufacturing waste by 2027
- 75% recycled or sustainable packaging and trim materials by 2027
What I like about these goals is that they are truly going to push us to innovate and take our circularity performance to new heights, all while being realistic enough so that these can come to life within our day-to-day operations.
How does Gildan plan to achieve the 100% sustainable cotton goal by 2025?
Presently, the majority of our cotton is being sourced from the U.S. We primarily buy U.S. cotton because of the inherent ethical and sustainable benefits that it has as a highly regulated crop.
A key, strategic partner for us towards achieving our 100% sustainable cotton goal is our partnership with The U.S. Cotton Trust Protocol® (USCTP) that we entered in 2021. The USCTP verifies and ensures, through rigorous data collection and auditing processes, that cotton produced is sustainable and has the lowest possible environmental risks. Over the next few years, we will increase the amount of verified cotton we purchase from USCTP towards achieving our 100% goal.
For the small amount of cotton sourced outside of the U.S., we will ensure it is sourced under the Better Cotton Initiative, a global nonprofit organization that aims to transform cotton production by developing better cotton as a sustainable mainstream commodity, and of whom we have been a member since 2016.
What about on the sustainable packaging front, are there any new and promising packaging techniques Gildan is looking at?
Packaging plays an important role in getting our products safely shipped from one place to another. We’ve seen some exciting developments in the past few years on this front and, I am certain, we will continue to see more developments in the future.
Right now, we are exploring options to use biodegradable plastic to package our underwear and sock products. For instance, we are already in the process of manufacturing recycled nylon swift tacks and 90% recycled inner pack bags.
We’ve also developed hangers made of bamboo. We will be implementing a pilot test to assess their readiness, and once finalized for use, we’re hoping to be part of the journey to eliminate the millions of plastic hangers created each year.
Gildan has set a goal to use 30% recycled polyester or alternative fibres/yarns by 2027. What kind of alternative fibres or yarns is Gildan looking at?
When it comes to recycled polyester or alternative fibres/yarns, we have an exciting journey ahead of us.
Currently, our main approach is to use less virgin polyester, and instead increase focus on recycled ones. Compared to making virgin fibre, recycled polyester fibre offsets using new petroleum, emitting fewer greenhouse gases, conserving water and energy in the process, and fostering more circularity in clothing production.
We've already begun some trials by introducing recycled polyester fibres into our yarn-spinning, and we’ll follow this fibre through knitting, dyeing, drying, and sewing to see how it reacts and performs to make sure we maintain the product quality and value our consumers expect. That’s the challenge when introducing a new fibre – we have to understand how the fibre will perform at each stage of our manufacturing process before implementing its use on a larger scale, something that our vertically integrated business model gives us the ability to do very well. The ability to incorporate more recycled fibres into our production not only allows us to use more circular fibre options, but also means that we can bring sustainability at large and make it accessible to everyone.
Last goal, but certainly not the least, how are you planning to reach zero manufacturing waste by 2027?
As I mentioned earlier, our investments in technology, such as the biomass system, play a significant role in reducing the amount of waste that we produce because we’re diverting our waste and creating something else out of it. By leveraging our vertically integrated supply chain and looking deep into the different parts of it, paying as much attention to what goes into the work as what comes out of it, and optimizing the resources we use, is how we plan to achieve this goal.
We also have other initiatives and programs that allow us to close the circularity loop in different aspects of our supply chain. As we work towards making our supply chain more efficient, continue to invest in technology and exciting innovations, and take active steps to close the production loop, I am confident that we are on the right path to reaching our zero-manufacturing waste goal.
To close off, what are some things you look forward to in Gildan’s journey to becoming more circular?
I’m very excited to see circularity take an even bigger spotlight at Gildan moving forward. It is such a vast topic, with endless areas to look at and optimize. From fibre, to waste, to packaging, circularity truly touches on the whole production cycle and makes this area a challenging and exciting one.
I look forward to seeing how Gildan’s circularity journey evolves to heighten focus on sourcing more sustainable and transparent raw materials, and enhancing sustainable waste management initiatives. We are on our way to becoming even more efficient and sustainable by embodying sustainability in every aspect of our operations.
To find out more about ESG at Gildan, click here.