Kohler's 2022 Believing in Better Report: Reducing Environmental Impacts Across Operations
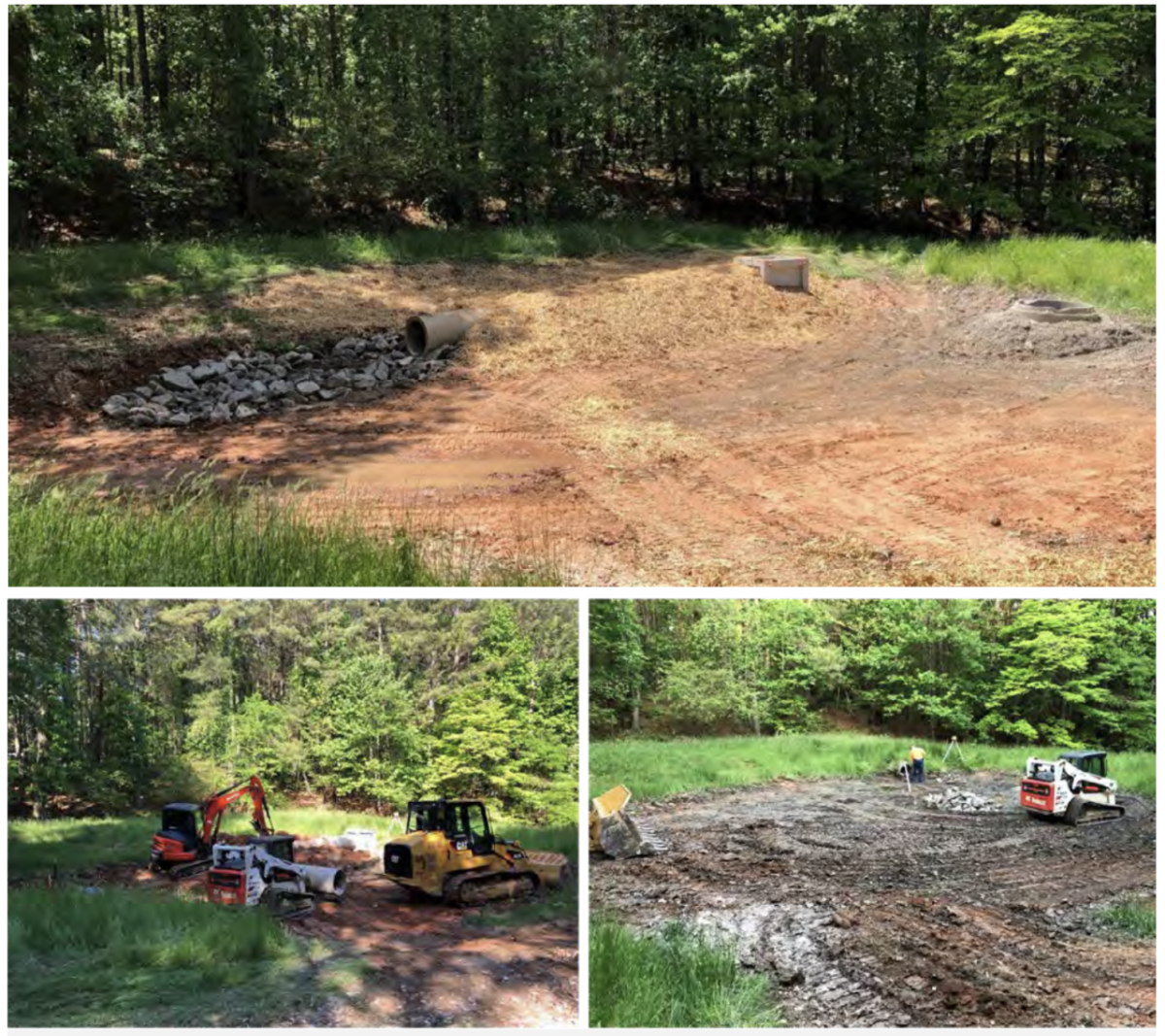
Originally published in Kohler's 2022 Believing in Better Impact Report
Reducing Environmental Impacts Across Operations
In 2022 we began evaluating operations in our manufacturing sites using the Design for Environment (DfE) process, resulting in tangible ways to advance our net-zero 2035 goals—including moving toward renewable energy, reducing water consumption, and reusing waste materials in new ways.
Every project considers many factors and the best ideas that come out of the DfE sessions are often unique to the particular process, region, or environment. Nine major projects were initiated, ranging from major equipment upgrades to entirely new greenfield installations. In 2023 we will expand this methodology throughout the enterprise and increase the number of projects that incorporate and execute DfE.
Kohler recognizes the outstanding accomplishments of our facilities through the internal Kohler Sustainability Excellence Awards. Facilities are eligible for the Kohler Sustainability Excellence Award though the achievement of their sustainability footprint reduction targets in the prior year. This award is given based on the assessment of several criteria, including the demonstration of high innovation, engagement with multiple stakeholders in the process, and the impact of their reduction.
Through emissions reduction initiatives, we have reduced our global net greenhouse emissions intensity by 62% since 2008 and by 17% in 2022.
GHG EMISSIONS REDUCTION
- We gather data and report on metrics according to the GHG Protocol, historically reporting since 2008 on scope 1 emissions (fuel consumed in our owned or controlled operations) and scope 2 emissions (generation of purchased energy obtained from our energy providers).
- We performed a climate risk assessment using scenario analysis to identify critical physical and transitional risks and opportunities that may impact our operations. We will use these learnings to deepen the integration of mitigation strategies to address these risks into our processes and operations.
GHG Reduction Success Stories
- Champagnole, France: Our plant reduced volatile organic compound (VOC) emissions by using an activated carbon filter system. For these efforts, it received a Kohler Sustainability Excellence Award in 2022.
- Brest, France: Our Kohler Power Systems facility switched fuel used in its test lab from conventional fossil diesel to fuels made from renewable HVO. This change enabled 13,000 liters of fossil diesel that were previously burned at the test benches to be replaced by HVO fuel, leading to a GHG emissions reduction of 31 metric tons, based on a conversion factor of 0.957 kgCO2e/kg. This effort will expand to the entire facility in 2023, with total GHG reductions projected at 864 metric tons.
- Juárez, Mexico: One of our largest facilities reduced GHG emissions by 6,600 metric tons and improved energy efficiency through many energy-efficiency projects. Its completed projects include reducing the use of compressed air, reducing natural gas use in kilns, and reducing the impact of defect repairs. This plant received a Kohler Sustainability Excellence Award in 2022.
- Brownwood, United States: Our plant created a Strategic Energy Management (SEM) plan with its electric utility Oncor to eliminate wasteful use of electricity by analyzing the power consumption of the plant and its equipment. The analysis determined that improved detection and elimination of compressed air leaks would help the facility reduce its power consumption by 1.3 million kWh annually, which is equivalent to preventing 921 metric tons of CO2e.
- Kohler, United States, & Andradas, Brazil: Our vitreous china sanitary ware plants identified process improvements that resulted in a reduction in kiln defects and lowered natural gas usage by 9% in our Wisconsin plant and 16% in our Brazil plant. This resulted in 1,155 MT of emissions saved collectively.
SCOPE 3 GHG EMISSIONS
In 2022 we made substantial progress toward implementing Kohler’s commitment, established by the Kohler Leadership Team (KLT) and Board of Directors in 2021, to report metrics and set targets for relevant scope 3 emissions, which are defined as all indirect emissions that occur in the value chain. Our Kitchen and Bath and Kohler Energy business units worked to identify what is material to our scope 3 emissions and we determined baselines that will be used to model future reductions and set targets, which will ultimately be combined into a company-wide scope 3 reduction goal.
Kohler’s procurement organization has three programs that address ESG with our suppliers. The Responsible Sourcing program reduces risk of potential forced labor with our suppliers by performing due diligence to the standards set forth within our Supplier Code of Conduct. The Supplier Diversity program supports the continued growth, increased visibility, and use of businesses owned by members of U.S. communities that are or have been historically—both socially and economically—underrepresented and underserved. Lastly, the Supplier Sustainability program focuses on improving the environmental sustainability of our supply base and purchased goods. Learn more in the Transparency section.
Clarke Energy Projects Reduce Scope 3 Emissions
Clarke Energy, a Kohler company, is a pioneer in biogas and converting landfill gas to power, securing 80% market share in this arena. Other successes include:
- They expanded to deliver 1.4 GW of biogas-fueled power globally, supporting sustainable waste management and renewable energy generation.
- They helped to reduce scope 3 emissions through energy- efficient combined heat and power (CHP) technology.
- They participated in several projects designed to help customers reduce GHG emissions through use of energy efficiency, emissions reduction, carbon capture, and renewable energy technologies. In Cambridgeshire, England, they will supply a CHP and water-source heat pump energy system for a greenhouse facility that will be used to grow 10% of the cucumbers consumed in Britain while using 30% less CO2 than a conventionally heated greenhouse.
- They will use CO2 recovered from exhaust gases to enrich air in the greenhouse to help accelerate the growth process, while waste heat generated from the system’s engines will be used to heat water circulating in the greenhouses. This project won the United Kingdom’s Association for Decentralised Energy’s Integrated Energy Award 2022 and was runner-up in COGEN Europe’s 2022 Innovation Award.
Clarke Energy is part of a consortium that won the 2022 Water Breakthrough Challenge sponsored by Ofwat, the water services regulation authority for England and Wales.
RENEWABLE ENERGY
Increasing the use of renewable energy sources across our global operations is another significant contributor to our ability to reduce Kohler’s scope 1 and 2 GHG emissions. Kohler continues to invest in renewable electricity to help reach our net-zero goal.
In 2022 100% of the electricity for our U.S. and Canada operations continued to come from renewable sources such as wind and solar. Kohler ranked 45th in the U.S. Environmental Protection Agency’s Green Power Partnership list of largest consumers of renewable power in 2022 with 393.6 million kWh of annual power usage in the U.S. coming from solar and wind. Kohler’s power purchases from Enel Green Power’s wind farms in Kansas, known as the Diamond Vista project, have reduced our global carbon emissions footprint by 27%.
Outside of the U.S., we have solar power installations that generated 30.5 million kWh of power in 2022. These installations include two new solar projects installed in 2022 in Saraburi, Thailand, that will supply 5,500 kWh annually.
WATER STEWARDSHIP AND REDUCING WATER USAGE
The stress on the world’s water supply is of paramount concern for Kohler. Water is not only used in our manufacturing processes, but it is also the means by which many of our products deliver experiences. We have reduced our water withdrawal intensity by 57% since 2008 a result of water- reduction initiatives.
We recognize the importance of reducing our operational water usage and being responsible water stewards. This includes restoration efforts in key high-water-stress watersheds where Kohler has facilities.
In 2022 we had 75 associates complete risk assessments of seven Kohler facilities located in high-water-stress locations and the surrounding communities to better understand water quantity, quality, access and biodiversity as well as river fragmentation.
The results of these assessments will be used to develop action plans around reducing water usage in operations and in the management of discharges to minimize impacts on groundwater and other water supplies.
Water Use Reduction Success Stories
- Beijing, China: Our faucet plant installed a smart water metering system this year to track and manage water more effectively in its processes. This project is estimated to reduce the facility’s annual water usage by 15%.
- Changzhou, China: In 2022 our faucet operations installed a zero liquid discharge (ZLD) system for its plating line that allows the facility to recover 90% of wastewater for reuse in the plating process, allowing the facility to rely less on higher-quality water sources.
- Tangier, Morocco: Our vitreous china facility completed a bathroom-improvement project that replaced pipes, valves, and fixtures, resulting in a 5% decrease in annual water consumption.
- Reynosa, Mexico: In 2022 our metal facility installed a closed-loop recycling system for fire protection to save water being utilized for weekly testing, eliminated the prewash stage for certain processes, and installed water- saving valves in the domestic areas. These projects reduced annual water consumption for these processes by approximately 45%.
Kohler Seed Fund Supports Stormwater Project
Kohler’s Spartanburg, South Carolina, property completed a stormwater project made possible by funding from Kohler Seed, a fund created to support associate-led sustainability initiatives. This sustainability project focused on modifying one of the location’s stormwater outfalls to ensure only clean water leaves the Kohler property—enhancing the watershed.
WASTE MANAGEMENT
Kohler is committed to responsible management of the waste generated in our manufacturing and hospitality operations worldwide. We have established a global goal of sending zero waste to landfill by 2035 and are implementing programs to reduce, reuse, and reclaim materials used in the manufacturing process.
These programs include finding new uses for manufacturing waste such as repurposing otherwise landfill-bound materials as the basis for new products. KOHLER WasteLAB®, which was discussed earlier in this chapter, has used landfill-bound pottery, wastewater sludge, foundry dust, and enamel powder to design and produce new products, with 25.5 metric tons of waste diverted from landfills through WasteLAB product sales since 2019.
We have reduced our waste to landfill intensity in our operations and offices by 58% since 2008, and in 2022 the reduction was 23% from the prior year. These reductions have been achieved through process improvements and diversion initiatives to reuse or recycle waste previously sent to landfill.
We have several facilities globally that are leading the way to net-zero waste to landfill. In 2022 six manufacturing facilities reported net-zero waste to landfill, with an additional five facilities that are approaching net-zero. Combined, this resulted in 8,313 metric tons of waste diverted from landfill. One of the facilities was Kohler Power Systems in Johor Bahru, Singapore. In addition to maintaining its waste segregation projects separating its largest waste streams, it has been actively working to transition its facility to phase out paper use by digitizing as much as possible. Another great facility initiative was our faucets facility in Cheltenham, U.K., which implemented a waste education program and expanded recycling sorting to make sure that associates segregated all waste streams.
Waste Reduction Success Stories
- Andradas, Brazil: Our facility made process improvements to reduce the amount of waste treated through its sewage treatment station, reduce the amount of sludge sent to landfill, and increase overall efficiency. Over the past two years the plant has achieved a 58.5% reduction in sludge generated per item and a 21.5% cost reduction.
- Champagnole, France: Our facility reused 919 metric tons of wood scraps from panels to heat the entire production site and office headquarters. It also reduced its waste disposal by 25% and decreased cardboard consumption by 4%. For these efforts, it received a Kohler Sustainability Excellence Award in 2022.
- Nanchang, China: Our faucet plant continues to increase the amount of waste materials recycled, including waste sand, sludge, plating wastewater, and waste filter paper, supported by an advanced wastewater treatment system with multistage reverse osmosis membrane and vacuum distillation technologies. The amount of non-recyclable waste produced at the plant has been reduced by 60% over a five-year period and the cost for processing of nonrecyclable waste decreased by 33%.
- Sariburi, Thailand: Our vitreous china plant automated its machine casting which reduced scrap clay by 1,130 tons per month and defective product by 111 tons per month.
KOS Green Cup
The annual Kohler Operating Systems (KOS) Cup competition highlights our associates in Kitchen & Bath manufacturing sites around the world and their commitment to continuous improvement across five categories, including the KOS Green Cup, which recognizes projects that reduce environmental impacts. In the 2022 competition nearly 200 project teams submitted entries in the regional competitions for projects completed over the past 12 months. The 2022 winner of the KOS Green Cup was our Nanchang faucets plant for reduction of non-recyclable waste.
Read the full 2022 Kohler Believing in Better Impact Report here.