How to Boost Industrial Safety and Productivity with a “Culture of Clean”
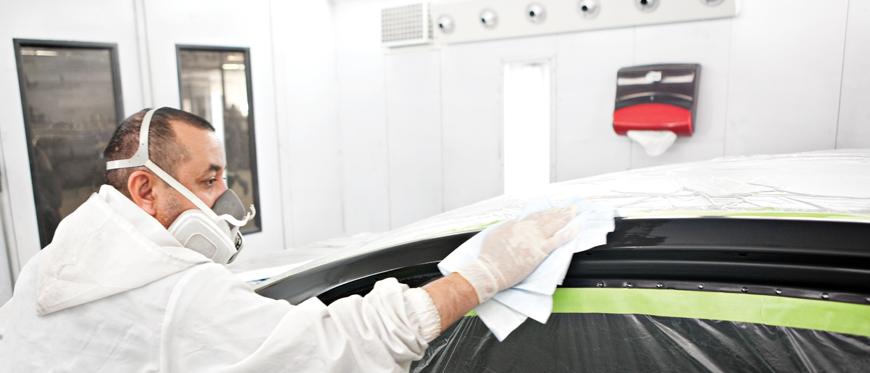
How to Boost Industrial Safety and Productivity with a “Culture of Clean”
Industrial workers aren’t afraid to “get down and dirty” on the job – but they’ll be happier, safer and more productive if their work environments are equipped to be kept as clean as can be.
This requires more than a once-in-a-while initiative of posters and pamphlets encouraging your workforce to be mindful of the mess. If you want to take full advantage of the business-building benefits of a cleaner work environment, it takes a new corporate mindset, from the corner office to the shop floor. Here are three key steps that will take you a long way down this often-overlooked path to a safer, more productive workplace.
Step 1. Create an Organization-Wide Culture of Clean
In many industries, workplace grit and grime are considered the normal cost of doing business — and if the issue of cleanliness gets addressed at all, it’s too frequently left to workers themselves. However, if managers across functions work in sync, enlisting the specific support of the top brass, they can create unified policies and programs that will emphasis the importance of clean to everyone, making it clear that it’s the responsibility of each employee, whether in the office area or on the machine line.
These policies and programs, however, must be more than a list of commandments from on high. They need to combine clear instructions and expectations – but they should also include corresponding recognition and rewards. In other words, HR should be just as involved as Operations or Maintenance.
Step 2. Commit On-Going Resources, and Reap Substantial ROI
Again, transforming your company’s culture isn’t a “one and done” effort. As a report from the Canadian Centre for Occupational Health and Safety points out, effective industrial “housekeeping,” as they put it, requires on-going attention, and produces significant benefits.
“Effective housekeeping can eliminate some workplace hazards and help get a job done safely and properly,” according to the report, which continues, saying, “Poor housekeeping can frequently contribute to accidents by hiding hazards that cause injuries… [it’s] not just cleanliness. It includes keeping work areas neat and orderly; maintaining halls and floors free of slip and trip hazards; and removing of waste materials (e.g., rags, cardboard) and other fire hazards from work areas. It also requires paying attention to important details such as the layout of the whole workplace, aisle marking, the adequacy of storage facilities, and maintenance.”
Of course, some may look at that list of requisite activities and immediately see them as costs. A recent survey by the National Safety Council, however, points to them as investments with high ROI, noting that “Over 60% of CFOs reported that each dollar invested in injury prevention returned two dollars or more.”
Step 3: Equip Your Employees with the Best Cleaning Tools and Supplies
Even the most inspired policies on cleanliness and safety won’t help you reach your goals until your organization is equipped to effectively implement those plans. As the report “Improving Safety Culture – A Practical Guide” concluded, “Without the right tools and processes in place on the production floor, accidents will keep happening, no matter how much safety training you provide.”
There are several important workplace truisms to observe here:
- Old supplies get old results. Consider the lowly, but still popular, shop rag. In spite of the facts that they clean less efficiently, they remain a fixture in many work environments. Try replacing them with more innovative products like disposable wipers, which research shows can reduce cleaning and maintenance time by as much as 35%.
- Healthier workers mean healthy savings. Modern cleaning products are not only more efficient; they are also more effective when it comes to dealing with potentially unhealthy chemicals. For instance, the disposable shop towels mentioned above release cleaning solvents much more evenly than do traditional cloth rags, and need up to 41% less solvent to do the job. This reduces employee exposure to substances which are sometimes toxic and which can impact employee health, time off and workers’ compensation claims.
And keeping employees healthy isn’t just the right thing to do – it pays at the bottom line, too. The National Safety Council reports that “Each prevented lost-time injury or illness saves $37,000.”
- Lowering the pressure raises productivity. It’s simple. Providing supplies that help do a job more quickly and easily helps workers get more done, with less stress. And happier workers are more productive workers.
Does your organization have a true “Culture of Clean?”
Sources
Tork
National Safety Council
Canadian Centre for Occupational Health and Safety
Dominic Cooper, Improving Safety Culture-A Practical Guide, 2001