Healthy Working: Ergonomic Safety at Gildan
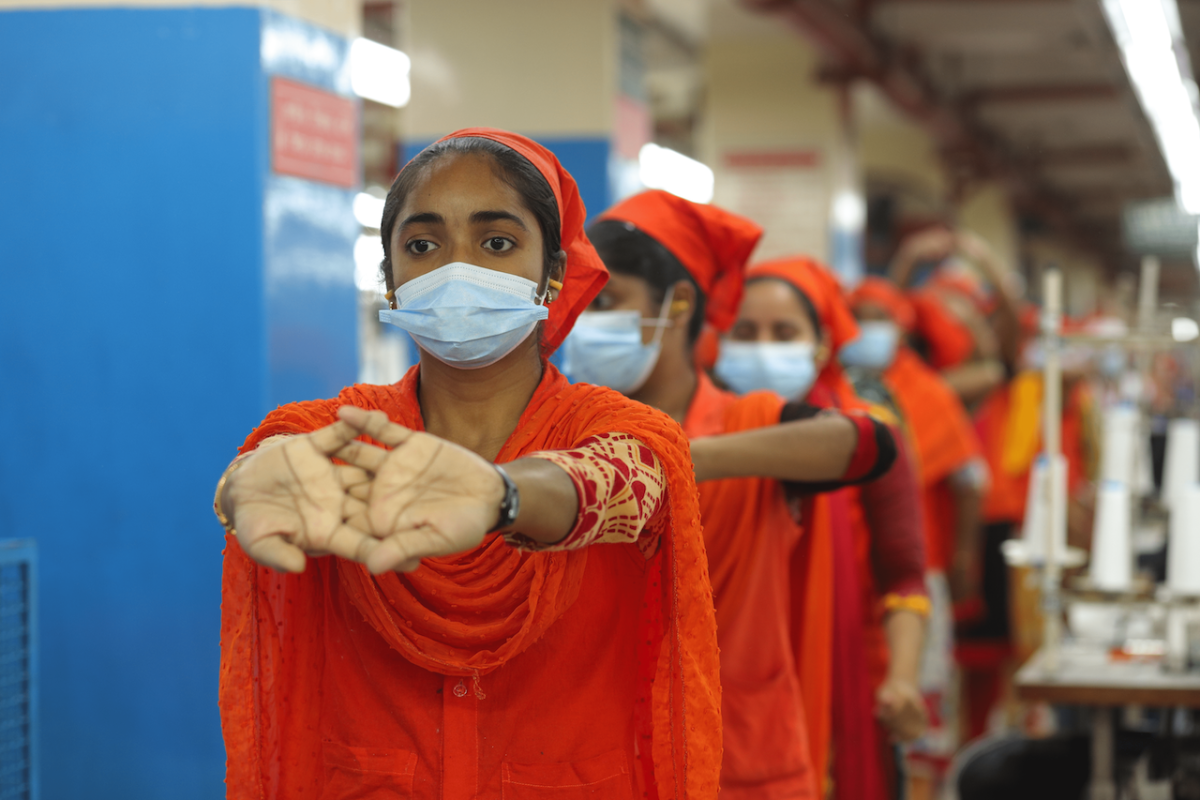
As a vertically integrated apparel manufacturing company, Gildan understands the responsibility that comes with supporting its global workforce of around 45,000 employees. One central element of this responsibility is ensuring that factory workers actively participate in our internal ergonomic care program to preemptively address the possible risks associated with a job and implement the necessary controls to safeguard workers’ health.
“The nature of apparel manufacturing can inherently expose our workers to repetitive movements, and they might slip into incorrect posture as the day goes on. This is why providing an ergonomics program that seeks to mitigate the long-term effects of physical work is extremely important for the well-being of our people,” says Honduras-based Gildan physician, Dr. Ana Ramos.
While the health and safety of its employees has been an important priority since the Company’s beginnings, Gildan’s ergonomics program was officially expanded in 2009 through a partnership with the Ergonomics Center of North Carolina (ECNC). The collaboration aimed at developing the Company’s Ergonomic Safety Guidelines, with an emphasis on recognizing and addressing ergonomic risks through training, ergonomic pauses, applicable engineering, and administrative controls. Following this partnership, Gildan put into effect several practices to promote health and wellness, such as including ergonomic pauses throughout the workday for sewing operators. These breaks reduce the physical effects these workers might experience due to repetitive tasks. Initiatives such as these are achieved and overseen by Ergonomics Committees, which have been instituted in many of Gildan’s facilities. These committees are comprised of the Company’s own responsibly trained workers in an effort to encourage a mindset for proactive ergonomic awareness in the workplace.
Since its inception, the ergonomics program at Gildan has expanded to provide employees with comprehensive prevention and awareness ergonomic healthcare. Along with preventative measures, the Company has established a fleet of specialized care clinics in its facilities across the globe to tend to its employees. At two of Gildan’s largest sewing facilities and at its textile complex in Honduras, on-site Back and Shoulder clinics are equipped with trained physicians and nurses capable of performing back and shoulder-related exercises for all workers in need of biomechanical strength, stretching, and flexibility help. In a continued effort to expand ergonomic services to more Gildan facilities, the newest Back and Shoulder clinic was opened in 2019 at Gildan’s Rio Nance complex in Honduras.
Looking Ahead at Gildan’s Ergonomics Program
Gildan strives to always grow with its workforce in mind, and this is reflected in its commitment to advance the Company’s ergonomics program. Gildan plans to develop new Global Ergonomic Guidelines that will reflect the Company’s goal of expanding the scope of its ergonomics program worldwide. Further, Gildan is on track to achieve Company-wide ISO 45001 certification at every one of its manufacturing facilities by 2028, which is an international standard for occupational health and safety, and which includes managing ergonomic risks in the workplace.
“The health and safety of our workers is a top priority, and that is why along with integrating ergonomic practices in our daily operations, we also provide medical care through clinics that are attached to our facilities,” says Mike Albright, Vice-President of Health and Safety, and Human Resources for Manufacturing at Gildan. “This way our workers know exactly where to find the support they need,” he finishes.
To find out more about Gildan's commitment to its people, click here.