Conflict Minerals Compliance Basics: Data Quality Control
Breaking down the basic terminology of conflict minerals compliance
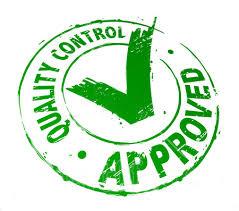
In this edition of “Conflict Minerals Compliance Basics,” we are covering data quality control.
Fact checking, data validation, and re-engagement are three of the most important pieces of any conflict minerals compliance program. Information provided by suppliers should be checked against data sources available via other projects and external sources (data mining sites such as the UN, US State Department, NGO’s, Industry Groups and more). As the names of companies within a supply chain are identified, they should be compared to a list drawn from external sources. This creates many additional benefits beyond conflict minerals compliance such as risk mitigation and brand protection from reputational harm.
Several steps may be implemented to help streamline the RCOI and hence the data assurance efforts.
Step 1: Have suppliers pass through a screening process. If they are able to provide a declaration that their products do not contain 3TG, provide them with the ability to exempt themselves from further inquiries.
Step 2: Suppliers that are not able to provide such a declaration should then be asked either to send a copy of their EICC-GeSI template or provide contact information for those parts and components that are likely to contain 3TG. As this information is collected it should be assessed for quality by quickly identifying possible errors and cautionary flags in line with the OECD Due Diligence Guidelines. Follow-up information should be requested whenever a problem is discovered within the information provided.
Step 3: Should the information provided contain errors or red flags, further information regarding the sourcing of these materials should be requested from the supplier.
Source Intelligence has implemented a data Quality Control (QC) process to check supplier data for accuracy, plausibility, consistency, gaps and reasonableness. The process consists of both automated and manual checks performed by software and technical personnel respectively.
During the QC process, several types of red flags may be raised which require business rules with regard to response and could potentially impact a customer’s risk. Our system happens to consist of three different types of flags: Signal, Warning and Red.
For more information request a free demonstration from Source Intelligence.