The Better Choice: U.S. Cotton
Q&A with Marc Doyon, VP Commodities, Gildan talks about the benefits of U.S. cotton
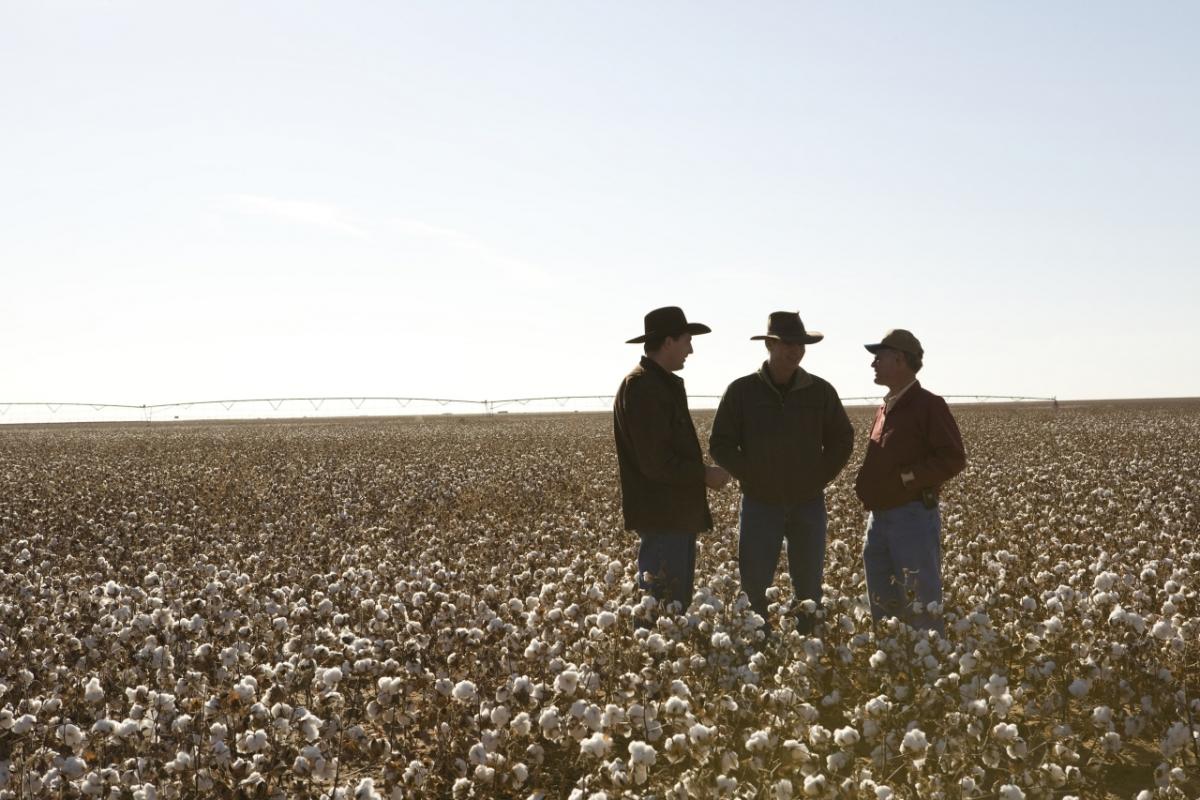
Marc Doyon, VP Commodities, Gildan Activewear talks about how sustainably-grown and ethically harvested U.S. cotton is the better choice.
Q: What do you feel are the benefits cotton offers as a fiber for garments?
The first thing is that cotton is a natural fiber and feels great on the skin. Cotton pulls moisture away from the skin on hot days and provides a soft, comfortable feel. Being a natural fiber cotton also means it is biodegradable at the end of a t-shirt's life, so it becomes natural fertilizer and provides nutrients back to the soil.
Q: Why do you choose to use USA cotton in your Activewear products?
There are many reasons we choose U.S. cotton and although it is very competitively priced, it’s important to note that price is not the most important one. U.S. cotton is simply the most efficient fiber for us to run within our yarn and textile operations from the perspectives of quality, consistency and cost.
The U.S. cotton crop is also sustainably grown and ethically harvested under strict USDA, USEPA and OSHA regulations so we have no concerns about the social and environmental responsibility aspects of the crop.
Another advantage is that U.S. cotton is grown closest to the largest market we sell into, effectively creating the most efficient transportation loop for our supply chain. We find U.S. cotton to be one of the world’s cleanest, with the least contamination, which makes it run more efficiently in our spinning mills and textile facilities.
Q: What makes US cotton a better choice?
The USDA grading system is extremely precise, so when we place an order for a specific set of criteria such as length, micronair, color or leaf content, we know our shipment will always match exactly what we ordered. This precision is very important to the overall process as it allows us to fine tune our yarn spinning and textile operations, so we are able to maximize production while minimizing waste and energy costs.
The U.S. cotton industry is supported by many organizations, including Cotton Inc, National Cotton Council and the USDA, which invest heavily in research and development and the pursuit of continuous improvement across all phases of the process. These organizations foster the promotion of modern farming practices and agroscience advancements that continue to optimize production to meet market demand while reducing the impacts to the environment.
Q: Can you describe the production process after the cotton is harvested?
After the cotton fiber is harvested from the fields it is sent to cotton gins, which are located in close proximity to cotton farms. In the ginning process, the cotton fiber is run through a series of rakes and combs to remove the leaves, bark and dirt which may have been picked up during harvesting. The resulting cotton fiber, called lint, is then wrapped and bound into 498 pound bales. In the ginning process, the cotton seeds are also extracted to be used as feed or used for the extraction of cotton seed oil in food products. In fact all the waste from the ginning is also repurposed into animal feed, bedding or composted into organic fertilizer for future crops.
Q. How are you able to get the quality of cotton that you are looking for?
Each bale is tagged with a unique identifier number (or Bale ID) and sent to a USDA warehouse facility. A small sample of the cotton lint from each bale of cotton is taken and sent to a USDA grading office where the sample is assessed for staple length, strength, micronair, color, leave contamination and other factors which are the most important qualifiers for the manufacturing of yarns. These measurements are recorded in the USDA’s electronic system, thus enabling the warehouse employees to pull exactly the quality of fiber to match individual orders as they come in.
Typically, cotton farmers sell their bales to merchants, sometimes in advance of harvest, and purchasers of cotton, like Gildan, enter into purchase agreements with the brokers for delivery of very specific quality of cotton fiber for use in our facilities.
Once the bale of cotton reaches our yarn-spinning facilities we will put the cotton fiber through a series of processes that seek to create the optimal blend of fibers for each of the specific yarns we are seeking to create. If we are looking to manufacture a finer ring spun yarn, we will be using better quality, longer staple length cotton as opposed to when we are producing a coarser open-end yarn.
Q. What are the characteristics of cotton that you look for in selecting your cotton?
Cleanliness is probably the most important factor. The main advantage of U.S. cotton is the efficiency of the equipment both in harvesting and ginning at removing contamination such as leaves, bark, dirt and any other foreign materials that cause issues in the processing of the cotton. The cotton fiber flows through a series of machines where the fibers are aligned before they are ultimately spun together to form a yarn. Some of the yarns we produce have the fiber running through rotors rotating at over 100,000 rpm’s. These fine-tuned machines do not respond well to contamination that could flow through with the fiber, therefore the cleanliness of our fiber is paramount at this stage.
Again, the selection of cotton depends on the intended fabric. Typically the coarser (or thicker) the yarn, the heavier the resulting fabric will be. Finer yarns, which go into lightweight fabrics require better quality cotton fiber, usually longer staple length and stronger. Ultimately, we want consistency in what we receive as it relates to what was ordered.
Q: Do you deal directly with farmers? If so, are you able to influence the crop profile from year to year?
No, we purchase the actual bales from brokers who negotiate and purchase the fiber from farmers. We do, however, engage continuously with farmers to facilitate the information we both need to plan our activities. Typically, we need to know what kind of yield they intend to have and understand the quality of the harvest. Farmers need to know what the demand for the product will be, as well as trends in price of competing fibers like polyester to determine quantities to be sown for the next year’s harvest.