The $20 Billion Business Case for OSHA
A groundbreaking new report proves that workplace inspections improves both worker safety and business' sustainability
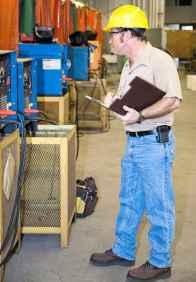
The study found that random inspections reduced annual injuries by 9.4% and lowered employers' medical costs by 26%, for an average of $350,000 in savings in the four years following the inspection. When applied nationally, this equals an annual savings of roughly $20 billion a year, even before calculating the reductions in pain and suffering. Research focused on inspections conducted by California's Cal/OSHA in a number of dangerous industries, finding that Cal/OSHA's randomized inspections fulfilled their intended purpose by substantially lowering not only injury rates, but also workers' compensation costs (when compared with matched workplaces that did not receive inspections), thus benefiting both workers and employers.
The research was conducted by Dr. Michael Toffel, Associate Professor of Business Administration at Harvard Business School; Dr. David Levine, Professor at the University of California Berkeley's Haas School of Business; and Matthew Johnson, Ph.D candidate at Boston University- Dr. Toffel reported on his team's research in a recent Harvard Business Review blog entry: "Workplace inspections not only improve safety, they cause no discernible damage to employers' ability to stay in business and no reductions in sales or credit ratings, according to our research. Nor did we identify any effects of workplace inspections on wages, total payroll, or employment." SAI asked Dr. Toffel and Dr. Levine for further comment on their findings:
Q: Based on your research - what were the areas where workplace inspections resulted in major cost savings? Was it surprising to you?
Dr. Levine: The costs we examined were workers' compensation claims costs. These cost savings are realized at workers' compensation insurance companies in the short term, and passed through to companies in the form of lower insurance premiums. Workers' compensation claims tend to compensate for medical costs and lost wages. But they don't compensate for all injury-related costs, such as the worker's pain and suffering and company's potential productivity decline while training a replacement worker. Thus the cost savings we identified are likely to underestimate the total.
Q: You mentioned in your article for Science Magazine how it has taken 40 years to generate robust evidence on the effects of OSHA inspections - can you expand on some of the challenges?
Dr. Toffel: Government agencies don't have a tradition of rigorously evaluating their activities. (By "rigorous evaluation" I mean using randomized trials or other methods of evaluation that have a credible comparison group.) Neither regulatory agency heads nor Congress has insisted on such evaluations. Politically, some appreciate an agency like OSHA and others oppose it for ideological reasons. Yet seldom does either group push for rigorous evaluations to prove whether or not their hopes or fears are well grounded. Such evaluations take years conduct, and few politicians or appointed officials have that long an horizon.
As for evaluating the effectiveness of OSHA inspections in particular, one major challenge is that most inspections target workplaces that recently had injuries or safety complaints, which makes it difficult to construct a similar control group of workplaces that had similar outcomes but were not inspected. Another challenge involves measuring outcomes. If you rely on the injury logs that OSHA requires companies to maintain, and if inspections lead some companies to improve the comprehensiveness of their recordkeeping, it is very difficult to identify the extent to which inspections affect injury rates versus injury recordkeeping. Our study overcame these two challenges by examining the impact of randomly assigned inspections on injuries that entered the workers' compensation system. OMB (US Office of Management & Budget) is pushing hard for more rigorous evaluations. If that gains traction, we might see more high-quality evaluations going forward.
Overall, these findings align with SAI's experience that workplaces compliant with the SA8000 Standard will see returns on investments, such as higher employee retention rates, increased productivity, lower accident rates, consistent product quality, and overall higher employee morale. Externally, safer working conditions lessen reputational risk for both brands and supplier factories.
In the wider context of OSHA, this article was also referenced during a recent OSHA briefing in New York, hosted by the Service Employees International Union (SEIU). The event featured two panelists- Jordan Barab, Deputy Assistant Secretary of Labor for OSHA, and Raphael Moure-Eraso, Chairperson of the U.S. Chemical Safety Board. Both addressed the report and its impact on validating the work of OSHA. These findings further support the words spoken last year by Dr. David Michaels, U.S. Assistant Secretary of Labor OSHA, at a hearing before the House Committee on Education and the Workforce Subcommittee on Workforce Protection when he stated, "We know that OSHA regulations don't kill jobs; they stop jobs from killing workers."