10 Resource Reduction Measures for More Efficient and Sustainable Biopharma Facilities
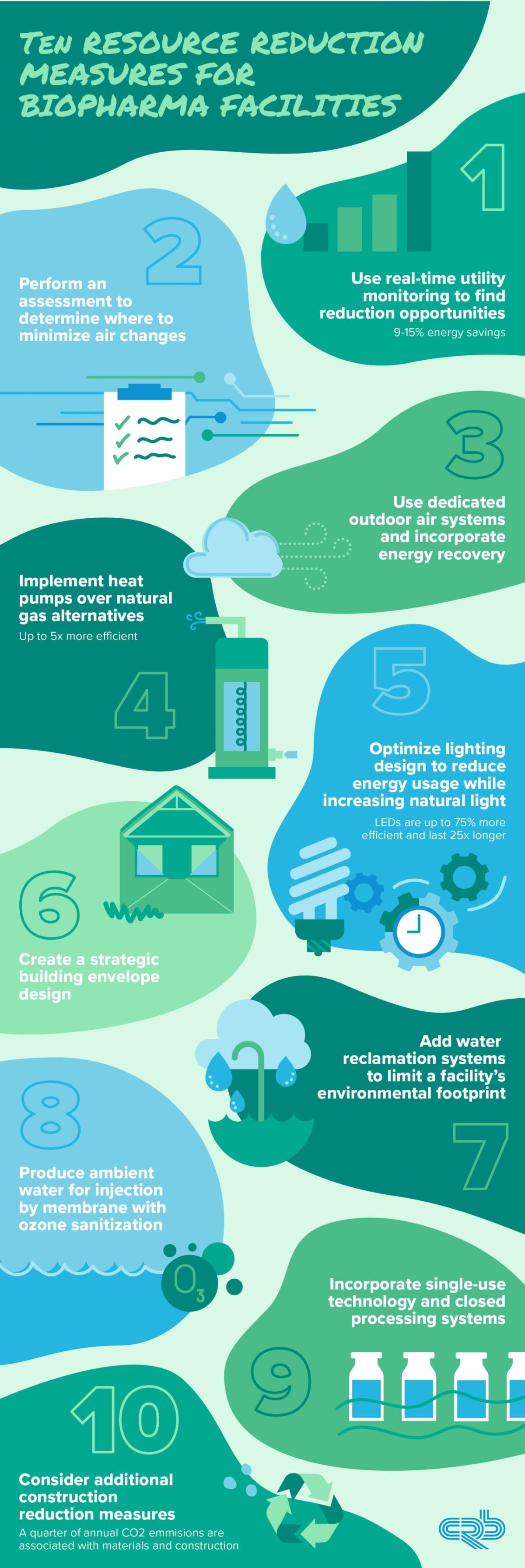
Resource reduction measures are solutions that can lead to lifecycle energy and cost savings for a favorable return on investment while simultaneously improving resiliency and promoting health and wellness in your facility.
Energy prices are volatile in the US and abroad. As companies expand operations, they are continuously looking for ways to decrease costs and improve their bottom line. Additionally, life sciences companies are committing to sustainability including goals for zero carbon operations and drastically limiting water consumption and waste production. Our recent U.S. survey of more than 500 life science leaders indicated that 84% of participants have sustainability benchmarking in place and over 75% of respondents would consider energy conservation measures and water reclamation strategies to reduce operation costs and environmental impacts. Many companies are aligning operations with the United Nations Sustainable Development Goals as well.
With these goals in place, the first step to achieving them is reducing your facility’s resource consumption. Applying best design and construction practices to go beyond “code minimum” and reduce the utilities necessary to run your facility not only advances your sustainability goals, but also makes your facility more efficient and can decrease operations costs.
We’ve discussed, in the past, that there are opportunities to reduce energy consumption by changing the source for your utilities, but the options don’t end there. The other half of the equation is determining where you can reduce the resources your facility uses. Many reduction measures focus on energy and carbon, but water and waste minimization are important to holistically reduce a facility’s footprint.
Here are 10 resource reduction solutions that you can implement today or plan for the future.
1. Use real-time utility monitoring to find reduction opportunities
Collecting data about your current utility usage is the best place to start; you cannot improve on what you cannot measure! The more information you have about your facility’s utility usage, the more you will be able to determine opportunities for reduction in the future.
Metering main utilities (electricity, gas, water) and submetering specific subsystems (including chillers, cooling towers, high purity water systems, steam production, and air handling units (AHUs)) provides crucial trend data to baseline facility operations. Benchmark utility assessments can help you identify low hanging fruit—or the easiest opportunities to cut out excess utility use—for your site.
As the life sciences industry embraces the move to Pharma 4.0™—ISPE’s initiative to introduce Industry 4.0 concepts and technologies to life sciences facilities—more manufacturers have already moved to more digitization and automation. These additions can produce real-time analytics that aid measuring and benchmarking. Implement a continuous monitoring-based commissioning (MCBx) software to collect, analyze and visualize data, which can help you optimize equipment performance and efficiency. A fault detection diagnostic system can identify system anomalies immediately resulting in energy savings ranging from 9% to over 15% and paybacks under five years.
2. Perform an assessment to determine where to minimize air changes
Air changes are important to maintaining air quality in cleanroom spaces and meeting GMP requirements, but this results in a high HVAC energy demand. It is possible to minimize air changes within regulatory standards. Reducing air changes in your facility lowers HVAC energy demand and creates cost savings.
During the design phase of new projects, perform an air change assessment to quantify particulate levels at various rates for the specific facility to determine opportunities to reduce air changes beyond legacy designs. Air changes can be minimized to meet GMP requirements at the lowest level without compromising risk.
For existing facilities, evaluate air change rates to identify if the system was balanced above design rates and can be rebalanced to initial design loads or be further reduced beyond the initial legacy design. If a facility has been operating for a few years without exceeding limitations, and particulate samples have never come close to limits, it may indicate the facility is over-ventilating and there are reduction opportunities.
Finally, you can achieve additional savings by validating spaces with reduced air changes for non-production and non-occupied hours, as well as using software to optimize ventilation rates based on changing particle conditions.
3. Use dedicated outdoor air systems and incorporate energy recovery
Life sciences facilities can realize large HVAC energy savings by decoupling ventilation and air conditioning with a dedicated outdoor air system (DOAS) incorporating heat recovery.
A DOAS brings in 100% outside air and conditions prior to distribution to downstream air handlers. The benefits of a DOAS include separating sensible and latent loads through humidity control, tempering outdoor air, satisfying ventilation and filtration requirements, and providing pressurization. Given the large dehumidification requirements for GMP spaces, life sciences facilities can specifically benefit from a DOAS because it reduces reheating and cooling loads. A DOAS can also be equipped with energy recovery strategies for increased savings.
Different energy recovery solutions can be implemented with a DOAS to recover energy from the exhaust stream and transfer it to the ventilation air. Energy, or enthalpy, wheels can exchange both sensible and latent heat, but run the risk of cross contamination between the airstreams. Run-around hydraulic loops can be used in place of an energy wheel to avoid potential contamination, but only recover sensible heat.
4. Implement heat pumps over natural gas alternatives
Heat Pumps are up to five times more efficient than traditional natural gas alternatives and can be powered by clean electricity for zero carbon design. They transfer heat from one place to another rather than generate heat and can use water, air, or the ground (known as geothermal) as an energy source or sink. Some heat pumps can generate both hot water during the winter and cooling water during the summer, and during simultaneous heating and cooling, heat can be recovered from the condenser and redirected for heating hot water or similar end uses for maximum efficiency, energy, and cost savings. Generally, the coefficient of performance (COP) of an air-water heat pump may be 2-3, and water-water may be 4-5, while a heat pump operating in heat recovery mode, simultaneously heating and cooling, can have a COP of over 8.
Furthermore, you can implement heat pumps with low temperature hot water (LTHW) systems that run at 140℉ or below to achieve additional cost and energy savings. LTHW systems reduce the thermal losses of a system and enable a wider variety of zero carbon heating alternatives. Also consider how refrigerant selection and climate can affect heat pump systems. Large scale heat pumps that use natural refrigerant and can operate reliably in sub-freezing temperatures are not mainstream today, but that is likely to change as new technology emerges.
5. Optimize lighting design to reduce energy usage while increasing natural light
Efficient lighting design can encompass the types of lighting you select, where you choose to put those lights, and also how much natural light you let into a space. Not that long ago, most life sciences labs and manufacturing spaces had no natural light, but recent trends have seen companies adding windows to the spaces to minimize energy usage while maximizing occupant health and wellness.
The first and easiest energy and cost-saving opportunity is updating the types of lighting used in a facility. As most people are aware, replacing existing halogen bulbs or fluorescent tube lighting fixtures with more efficient, longer-lasting LEDs can reduce lighting energy and excess heat emitted in a space. LEDs can be up to 75% more efficient and last 25 times longer than other lighting alternatives.
However, additional lighting strategies exist for increased savings.
For non-GMP spaces, use occupancy controls to ensure lights are off when nobody is present. Occupancy controls can also respond to room temperature and turn down HVAC systems through air exchange reduction for energy optimization.
Lastly, daylight harvesting systems, which intelligently maintain proper lighting in a space by supplementing electric lighting with natural lighting, can save additional energy. The added benefit of daylight harvesting is that maximizing natural light can improve occupant mood, circadian health, and productivity.
6. Create a strategic building envelope design
A well-designed building envelope has significant potential to reduce energy use for heating and cooling. Maximizing insulation, limiting infiltration, and selecting innovative window solutions can all prevent thermal losses, save costs, and create a more comfortable internal environment.
Consider insulating buildings beyond code minimum; this is likely to produce a return on investment in lifetime energy savings. Another option is a cool roof, designed to reflect sunlight rather than absorb solar energy, which reduces air conditioning needs and lessens the urban heat island effect. Alternatively, green roofs for office spaces can aid with stormwater management, while creating more enjoyable roof spaces. For facilities with joint office spaces and lab/GMP spaces, be sure that green roof spaces are not located in the wake of exhaust streams. Finally, if possible, consider building orientation during design to best take advantage of natural light while avoiding glare and unwanted solar heat gain.
Outdoor air infiltration can pose a challenge to building systems regulating the inside environment. A tight envelope with air barriers to limit infiltration can save energy, reduce moisture, and increase HVAC system efficiency. Limit infiltration with continuous door and wall seals, double doors, automatic pressurization, and air curtains over entrances.
Finally, windows are a crucial part of the building envelope and emerging innovations minimize glare and heat loss, while maximizing window area for occupant wellbeing. Window solutions include multi-pane systems with glazing, electrochromic windows that adjust tint dynamically to environmental conditions, and window films that provide insulation or can harness solar energy.
7. Add water reclamation systems to limit a facility’s environmental footprint
Resource reduction isn’t limited to energy; reducing water is another important consideration to save costs and preserve valuable resources. Most life sciences facilities employ significant amounts of water, as it is an integral part of the manufacturing process, thus water reclamation can help limit overall city water consumption. Reclaim options include stormwater harvesting, air handler condensate collection, and reverse osmosis (RO) reject water that can be directed to a storage tank and then used on-site, including cooling tower makeup water and irrigation.
Consider adding air-water-water heat pumps which offer water savings by using the air as a heat source/sink. These also eliminate the need for cooling towers and related equipment, which frees up more space for manufacturing. Heat recovery chillers can limit cooling tower operation by redirecting heat to the hot water system during simultaneous heating and cooling operations. Air-Cooled chillers can also eliminate cooling tower usage for central plants, but these are less efficient than water cooled alternatives. They can be considered in cases where water savings are of higher concern than energy savings.
8. Produce ambient water for injection by membrane with ozone sanitization
Traditional WFI production through distillation is often one of the largest facility consumers of natural gas and water. Although vapor compression distillation uses less utilities and requires less pretreatment than multi effect distillation, it still requires steam. Membrane ultrafiltration-sourced water for injection (WFI) generation reduces utility needs while maintaining manufacturing quality and saving manufacturing space.
In the process of producing ambient WFI by membrane with ozone sanitization, water is pretreated before purification with RO and then passed twice through a thin membrane before electrodeionization and ultrafiltration to achieve the effective endotoxin reduction. Downstream, the storage and distribution system can use ozone at ambient temperatures for routine sanitization instead of hot water methods. Membrane systems often take up less space and require less welding for decreased installation complexity and cost.
Finally, ambient WFI can be used for production, with point of use steam free heating methods, like a thermal fluid skid or electric heat pump, to eliminate plant steam needs for WFI.
9. Incorporate single-use technology and closed processing systems
The combination of single-use technology and closed processing systems can lessen utility use associated with cleaning manufacturing equipment and spaces. While single-use technology does come with an environmental trade off, it still may be a better option for some facilities, based on specific reduction goals.
As the industry is increasingly pressured to deliver products faster while reducing overhead costs, single-use technology is becoming more popular. Single-use technology can improve flexibility while saving energy and water through avoiding sterilize-in-place (SIP) and clean-in-place (CIP). However, plastics for life sciences applications must be robust enough to not adulterate the product and are often harder to recycle, so single-use technology generates more plastic waste and requires resources to transport and dispose of plastic off-site. It’s possible to minimize waste by repurposing plastics for certain test runs or shredding and sterilizing material for new applications such as construction materials.
Single-use technology can be integrated into closed processes, relying on pre-sterilizing or gamma irradiation of the components and avoiding the cleaning and sterilization steps that hard metal solutions typically require. Closed process-in-a-box systems are positioned to transform cell and gene therapy manufacturing because of they can maximize a facility footprint for manufacturing, eliminate cleanrooms (and their support spaces) altogether, and scale production cost-effectively.
10. Consider additional construction reduction measures
Construction methods and material selection are a critical part of facility development and reduction measures can reduce a project’s footprint while expediting project delivery. Buildings contribute to 40% of annual CO2 emissions; a quarter of these emissions are associated with materials and construction, also known as embodied carbon. Choosing low-emitting building materials and reducing resource consumption during construction is crucial.
When it comes to materials, reduction measures include repurposing existing materials for renovation, using recycled materials, and specifying materials with low levels of volatile organic compounds and environmental product declarations. This can lower embodied carbon and increase air quality for building occupants. Also consider this for materials such as paints, adhesives, flooring, insulation and furniture.
Responsible on-site construction practices can also limit a project’s footprint. Waste management and recycling plans, paperless job sites, LED temporary lighting, and future electric equipment combined with solar panels on trailers can reduce resource consumption during construction.
Another option is PPMOF construction methods (prefabrication, preassembly, modularization, off site fabrication), which are becoming the new normal in the industry. PPMOF construction offers many advantages, including schedule acceleration, cost certainty, quality, safety and energy conservation by taking advantage of an off-site, streamlined construction environment. PPMOF is a collaborative effort and requires the entire team to plan and scope the project. Integrated product delivery and lean construction strategies can be used to successfully bring together project stakeholders from the start.
Planning is key
This list only scratches the surface of what is possible for efficient facility design and construction. These solutions are proven technologies and many facilities have implemented them for energy and cost savings. While no single solution is perfect, planning is key to navigating the tradeoffs between technologies. For example, campus sustainability master plans and equipment lifecycle utilities assessments can identify resource reduction solutions and schedule them with the expected lifespan of existing equipment. This allows you to maximize existing resources and coordinate projects to minimize downtime.
Understanding which projects should be prioritized for your facility or when is the best time to implement these solutions for project synergy requires an interdisciplinary and experienced team that sees a project from design through construction. As part of such a team, CRB is here to help. If you are interested in decreasing your facility’s resource consumption and operational costs while maximizing production, let’s chat.