Food and Beverage Leaders Turn to Renewable Energy, Circular Solutions for Cost-Savings
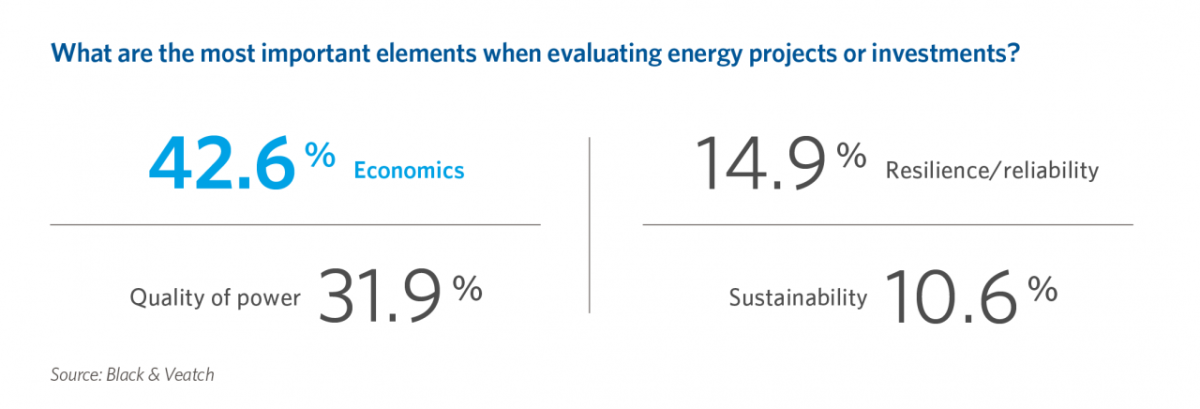
Food and Beverage Leaders Turn to Renewable Energy, Circular Solutions for Cost…
By Zack Olson, Founder, NextGen Agriculture; and Chris Vigil, Project Manager, NextGen Agriculture
From food safety and regulatory compliance to packaging and supply chain logistics, the food and beverage industry is constantly hunting for solutions that balance profitability and sustainability. With market share increasingly on the line – particularly for large consumer goods companies – food and beverage companies are being squeezed to analyze every cost.
A 2018 study by market research firm IRI found that since 2013, more than $17 billion in consumer packaged goods (CPG) industry sales have shifted from large brands to smaller ones. This is particularly true for “extra small” brands – those with annual sales under $100 million – who saw sales rise 4.9 percent. In comparison, large brands with annual sales over $5.5 billion only squeaked up 0.6 percent.
Brands with less than $1 billion in sales saw their market share rise from 23.5 percent in 2013 to 25.7 percent in 2017; large players saw a 2.2 percent drop during that same period.
This doesn’t paint a glowing picture for the food and beverage industry, as they face declining market share and rising production costs. To manage these challenges, companies are looking for ways to wring out every possible efficiency, and energy management – which can help reduce overall operating costs – instantly comes to mind.
Energy Meets Economics
Producing food and beverages on a commercial scale is inherently energy-intensive across the entire supply chain. Growing and sourcing ingredients, shipping them hundreds or thousands of miles, and using copious amounts of process heat and cooling all requires massive amounts of power. Add in packaging and distribution transportation along with basic facility needs – lighting, HVAC, refrigeration – and it becomes clear how energy can consume a substantial chunk of a company’s operating expenses.
According to Black & Veatch’s 2019 Strategic Directions: Commercial & Industrial Report survey, which polled representatives from across various commercial and industrial (C&I) sectors, the industry overall is taking a closer look at energy management. When looking at how companies spend their money on energy, lighting, heating and cooling, and production demands were named the most energy-intensive components of producing food and beverages.
Considering the amount of capital that goes into these investments, it’s no surprise that economics remain the primary driver when it comes to evaluating energy projects and/or investments, according to survey results. Respondents named economics the most important factor, followed by quality of power, resilience/reliability and sustainability.
From Monitoring to Renewables, an Industry Looks for Solutions
So what are companies doing to ensure lower energy costs? The majority of respondents (61 percent) are considering investing in electric efficiency upgrades, although 59 percent have made these improvements over the past three years. A little more than half (59 percent) are managing and monitoring energy consumption using software (e.g, SCADA), and 50 percent have conducted an energy audit in the past three years.
To a lesser extent, respondents are also partnering with local utilities on demand response programs (37 percent), thinking about or increasing onsite generation (22 percent), investing capital in onsite power generation (17 percent), working on an energy master plan, purchasing energy from a supplier or power purchase agreement (PPA), and managing energy use through a third party (11 percent).
Of those respondents considering onsite generation, more than half (54 percent) have either considered or are considering onsite renewable power sources such as solar PV, battery storage, CHP, wind, geothermal, hydro and bioenergy.
Ensuring that energy projects and/or investments provide solid ROI will be a driving force behind any decisions. But if the conditions are favorable, renewable energy could offer salvation when it comes to using energy more sustainably in production processes. The European Resource Efficiency Knowledge Center (EREK) says that renewable energy has “strong potential” across the food and beverage industry, particularly wherever there is a demand for heating; and that the industry can generate renewable heat through solar PV systems, biomass and biogas.
One subset of the food and beverage industry – the brewing industry – is making incredible strides when it comes to implementing renewable energy. In Hawaii, where energy costs are the highest in the nation, Kona Brewing Company and Maui Brewing Company are actively investing in solar PV and battery storage to power their brewery’s needs.
Kona Brewing, in partnership with EnSync Energy Systems and Holu Energy, is building a new facility that will include a massive solar-plus-battery storage system comprising 336 kW of roof-mounted solar paired with a 122-kwH battery, to supply 25 percent of the brewery’s total energy needs. Maui Brewing is taking it one step further, planning to rely on roof-mounted solar panels, Tesla battery storage and biofuel generators to become fully grid-independent by the end of 2019.
Investing in the Circular Economy
Food and beverage companies are also looking for ways to do more with less – in effect, finding new ways to monetize waste and side streams. Some breweries are embracing combined heat and
power (CHP) to offer onsite power generation and reuse a traditional waste stream. New Belgium Brewing, based in Fort Collins, Colorado, relies on two CHP engines that are powered by biogas from an onsite Process Water Treatment Plant, with a similar CHP facility under construction at the brewery’s Asheville location.
A number of breweries are also working to recapture carbon dioxide (CO2). As a byproduct of the fermentation process, CO2 is all too often discarded into the atmosphere. But through increasingly efficient and cost-effective CO2 recovery systems, breweries can now recapture the waste CO2 and put it to use in-house (e.g., carbonation), rather than having to purchase it from a third-party supplier.
Black & Veatch is also working with a client to up-cycle pre-consumer organic waste from food producers by converting the organic waste back into food ingredients via a proprietary bio-process. Returning this organic matter back into the food system provides a higher value use of the waste stream than composting or energy recovery. As more states follow the example of California, which has legislated mandates to divert organic waste from landfills, the need to apply technologies for organic waste handling will become more common.
Putting energy management measures in place – embracing renewable energy and on-site power generation and looking for ways to reuse traditional waste streams – will become more prevalent across the food and beverage industry as the technology becomes more affordable, and as companies work to decrease their carbon footprint and achieve sustainability goals.
Energy Use in the Cannabis Industry |
---|
Although marijuana remains a Schedule I drug at the federal level, it holds legal standing in a number of states, which have spawned a booming marijuana cultivation industry. As more growers hang their shingle, local utilities are feeling the pressure of this new demand. According to New Frontier Data, electricity consumption is expected to jump 162 percent by 2022. Cultivation is inherently energy-intensive, with the practice occurring in a variety of environments (e.g., homes, greenhouses, warehouses and open fields) under a wide range of skills, knowledge, experience, irrigation and lighting techniques, and capital investment. Last year, The Cannabis Conservancy, an industry advocacy group, issued its Energy Use in the Colorado Cannabis Industry report, which took a hard look at energy and water use within Colorado’s marijuana industry. According to the report, the industry used between 355MWh (low end) and 1,115MWh (high end) to produce marijuana last year, depending on efficiency. To put this in perspective, the entire state of Colorado used 54,418 MWh of electricity in 2016 – meaning that the marijuana industry potentially used 2 percent of the state’s annual electric generation. With this cost in mind, energy efficiency becomes incredibly attractive for the emerging marijuana industry. |
About the Authors
Zack Olson leads the NextGen Agriculture initiative at Black & Veatch, focusing on providing engineering and construction solutions to innovators working in food and agriculture technologies, including controlled environment agriculture and advanced greenhouse solutions.
Chris Vigil is a Project Manager for the NextGen Agriculture initiative at Black & Veatch. With a background in food and beverage and distribution and warehousing, Vigil is responsible for delivering successful project execution.