3D Printing Gets Fashionable
How Danit Peleg revolutionized the fashion industry with 3D-printing technology.
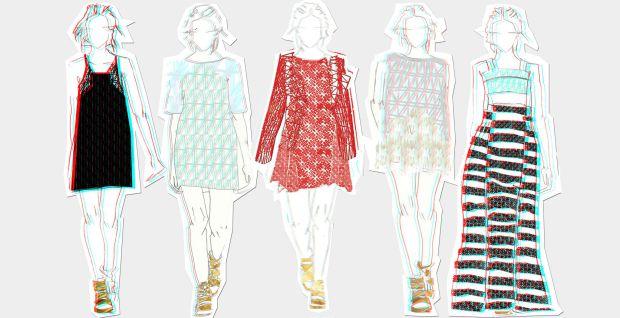
Danit Peleg | Fashion Designer
This Q&A is derived from Part 2 of a five-part white paper series called Routes to the Future, in which we explore the innovations, challenges and opportunities in a new era of possibilities.
Today’s shopper expects seamlessness and efficiency — and new technologies are helping retailers deliver on these expectations in new ways.
From virtual fitting rooms to clothing subscription boxes, the fashion industry is evolving to help shoppers find a perfect style and fit with little hassle.
Fashion designer Danit Peleg is exploring the intersection of fashion and technology by experimenting with 3D-printed clothing. Peleg foresees a future where your outfit can be printed at the click of a button – customized to look and fit the way you want.
Longitudes sat down with Peleg to discuss how she started 3D printing clothes and where she sees the fashion industry heading with this technology.
Q: In your TED talk, you mention experimenting with leftover, ‘weird’ materials. What materials have you printed?
A: Over the past four years, I studied fashion design and realized that I enjoyed creating my own textiles and experimenting with different fashion technologies. For my final project, I needed to create a full collection so I decided to research 3D printing.
I knew nothing about 3D printing when I started my project, and there were different challenges I had to solve along the way. The main challenge was finding the right filaments to print. The key property for a textile is flexibility, and it was really difficult to find filaments that were flexible and actually comfortable on the body.
For a month, I experimented with a material called PLA, which was very stiff and breakable, but I thought there could be a way to use the PLA on the outside with a flexible structure on the inside. I didn’t get too far with it.
The breakthrough moment was when I was introduced to FilaFlex – the filament I ended up using for my collection. It’s extremely flexible, strong and sustainable. And it was really new – they had just introduced the filament when I discovered it. My textile turned out to be flexible, fun and bouncy.
Q: Can you describe the ‘aha’ moment when you realized you could 3D print clothing?
A: Oftentimes I find inspiration for my creations in events from my life. I went to a festival called Burning Man and met this random guy who gave me a necklace.
I put it on and realized that the necklace was 3D printed. The rest of the week at the festival I kept looking at the necklace and thinking about how this guy probably created hundreds of necklaces with stacks of printers.
I realized that people already have these 3D printers. So why couldn’t I start printing clothes with it? I did some research online and saw that no one had done it. I wondered why. So I was curious and started experimenting.
Q: Tell us about your 3D-printed fashion line.
A: My inspiration for the whole collection was from a painting by French artist Eugene Delacroix called Liberty Leading the People. Having a French background, I felt really empowered by the idea of taking this classical painting from a different era and bringing it to life.
I actually modified the painting so it would look like a 3D image. I used the triangle that’s in the painting composition as the main motif of my collection. That’s why the red jacket has all of those triangles.
I chose to put the words liberte on the back, which means freedom in French because I felt so free and empowered that I could design and create this jacket myself in the studio of my house in Tel Aviv. I didn’t need to work or meet with anyone else to make it happen.
My entire collection was printed with FilaFlex except for the heels of the shoes, which were made with the hard material, PLA. The Liberte jacket was the first garment I ever 3D printed, which made me really attached to the item.
The cool thing about the jacket is you can easily change the words to something else such as your name. In the future, you could probably even choose the materials you want to print the jacket with. It’s kind of interesting to see how this customization is completely digital, and that’s what gave me more energy to continue exploring this technology.
Q: How far are we from easily printing our clothing from our own home?
A: Each month, these printers are getting faster and cheaper, and more people are actually buying them for their houses and understanding what they can do with them. I feel like once more materials can be printed, it will change a lot for the fashion industry.
There’s just so much you can do with 3D printers. We will probably see them in supermarkets soon. I think it will become a common household item like a microwave or TV. I think in 10 years things will look completely different for 3D printing.
In terms of cost, the most expensive thing is time. The Liberte jacket took me around 300 hours. But this year, I’m using a newer version of the printer called the Witbox 2, which will print the jacket three times faster than the older model. It should only take me 100 hours this year. The material itself is not that expensive. It’s really the time that’s expensive.
Q: How do you think this technology will impact the retail and fashion industries? How will designers, manufacturers or distributors have to adapt to a new model?
A: There’s actually a lot happening with current technology that’s changing the fashion industry. For example, there’s an app where you can take two pictures of yourself and get all your measurements without having to meet somebody in person.
With my designs being completely digital, I can customize any design to any body measurement. For example, I created a dress for a dancer in the opening ceremony for the Olympics in Rio.
I never met the dancer before. She was from the U.S. I was in Tel Aviv, and the event was in Brazil. Just by using the app, I made a dress that was completely customized to her body, and it fit like a glove when she tried it on at rehearsals.
From the design side, it saved me so much time. I didn’t have to make a million samples. The dress for the Olympics actually inspired me to extend it into a full collection that I am going to launch in a month.
I can tell you that while working on this collection, I had almost zero waste. From a sustainability standpoint, the fashion industry has always had a big impact on the environment.
Let’s say this technology grows rapidly and we can print patterns and create materials we can actually wear and wash regularly. Then consumers will actually seek out this kind of clothing because it’s convenient and customized to them. In the future, when these printers are in your house, I can send you a file and you can immediately adjust the file to speak to your measurements.
Q: And the shopper can choose the material?
A: You can choose the material, whether it’s cotton or wool. And while you’re getting ready in the morning, you can just press print and have the dress done by the time you’re done getting ready. I think fashion designers are always ready to adapt to new ideas once they have access to the technology they need.
The world is changing, and they know they need to adapt. Fashion designers will love the idea that they can make a dress exactly like they envisioned. In fact, I’m currently pushing the boundaries again by mass producing 3D-printed clothing to sell.
By mass production, I mean about 100 jackets. The customer can come to my website and customize the jacket completely, including picking the color of the lining, choosing the color of the 3D-printed textile and customizing it to their own measurements.
Hopefully, in a month, this conversation won’t be science fiction. It will be a reality in which people can buy 3D-printed garments and customize it to their preferences and body.
Editor’s note: If interactive links in the report are not functional, please clear your cache and re-download the report.
This article is part of UPS Longitudes' Routes to the Future series, which explores the nusiness and technology trends that will shape our world in the next 10 years.
This article first appeared on Longitudes, the UPS blog devoted to the trends shaping the global economy. Subscribe here to receive new content.